Drinking a cup of coffee on deck of vessel Skandi Skansen with a view of suction anchors is a notability. Recently the anchor installation campaign for Equinor’s Hywind Tampen windfarm in the North Sea was completed with Skandi Skansen. Eleven turbines with a combined effect of 88 MW stands to be the largest windfarm in the world.
SEMAR has been involved in planning and execution of the operations together with Dof Subsea. Life at sea can be thrilling, educational and hard work.
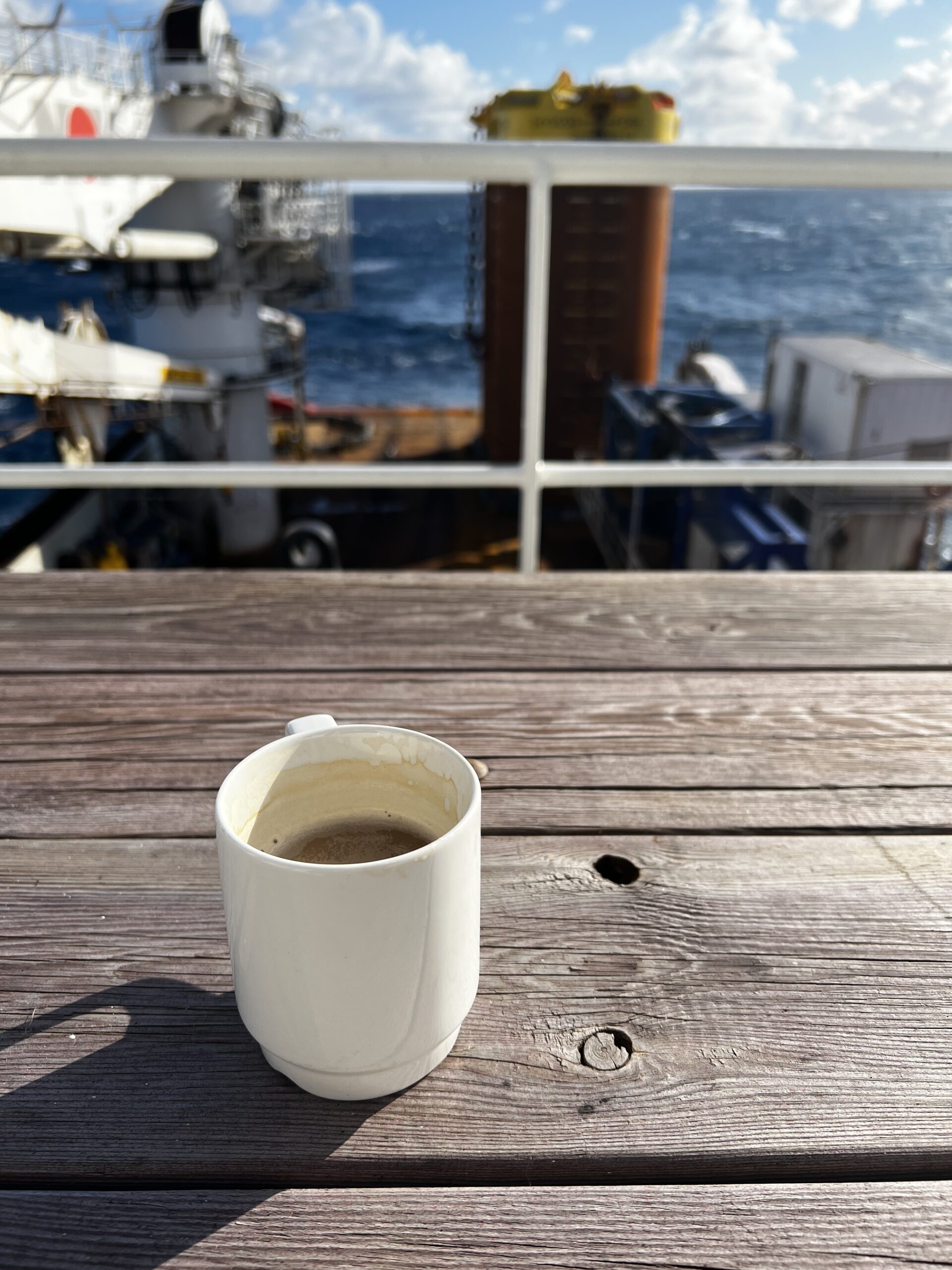
A cup of coffee with a view of a suction anchor
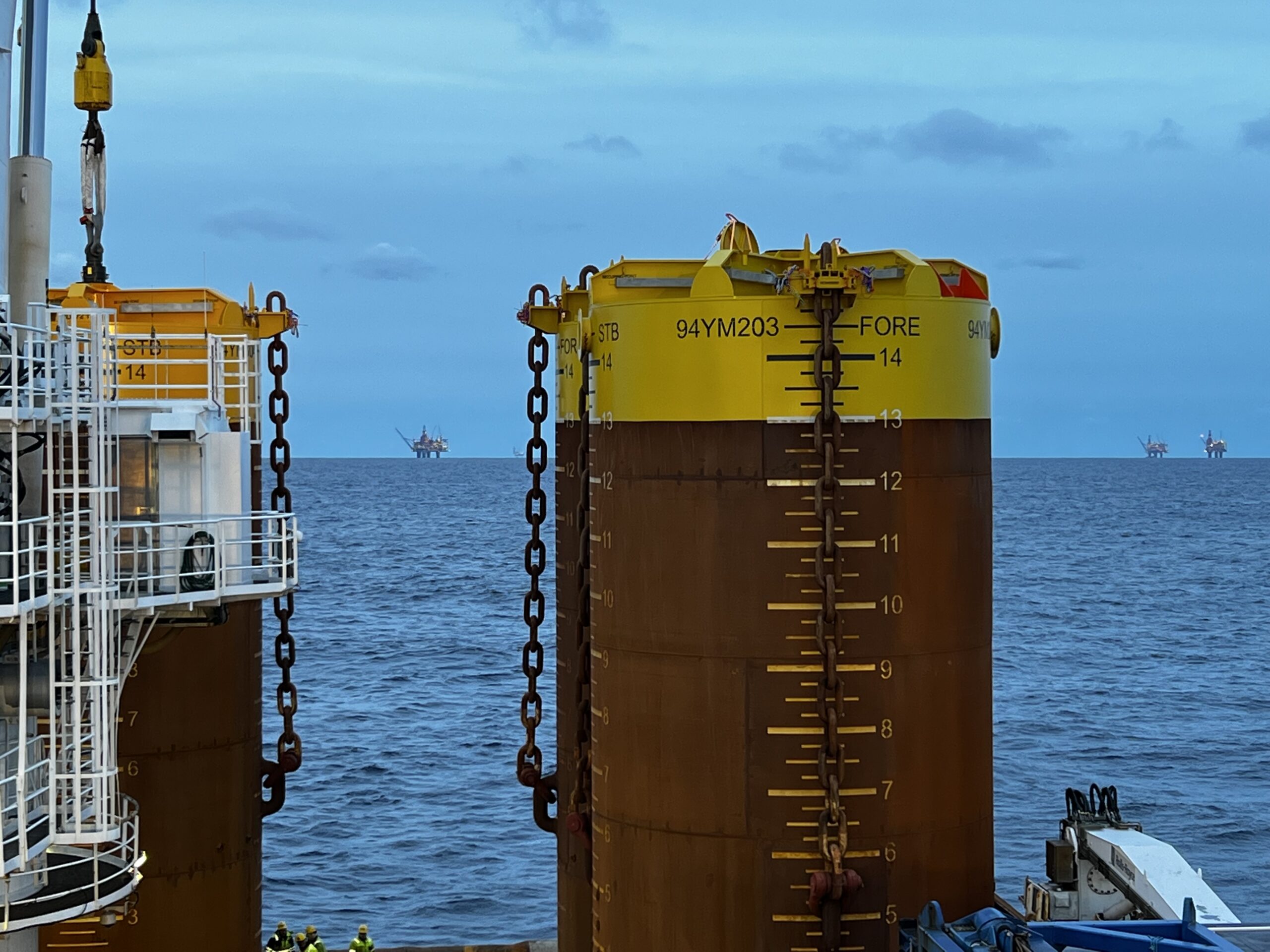
Suction anchors in front of the Gullfaks platforms
From site at Tampen there is a clear view of the Gullfaks platforms in the south and Snorre in the north. Wind turbines will supply nearby platforms at Snorre and Gullfaks oil fields with electricity.
The Hywind Tampen project is an example of how the knowledge and resources gathered through years of experience from the offshore oil and gas industry can be utilized to accelerate development of new offshore technology. The suction anchor is well known and proven technology – however there is room for innovations.
A smart anchor sharing strategy was utilized by Equinor which gives cost and material reductions. The project will provide useful information for further developing smart solutions for offshore floating wind turbines in all stages of the engineering.
Before easter, SEMAR performed mobilization activities for the anchor installation campaign. The mobilization for an offshore campaign needs to be well planned as it is important to ensure that all equipment is loaded and properly secured on the vessel before departure.
The main part of this mobilization was to install the anchor grillage and seafastening system designed by SEMAR. The anchor seafastening system is used to securely attach the anchors to the vessel deck for transportation to field. One great part of working as an engineer on marine operations projects is the opportunity to experience and integrate all parts of the operational phase; from planning and analysis, to preparation and follow up of operations on deck.
It is great fun when operations go well. Loading the first anchors was more or less and exam for our design and it all went smoothly and as planned.
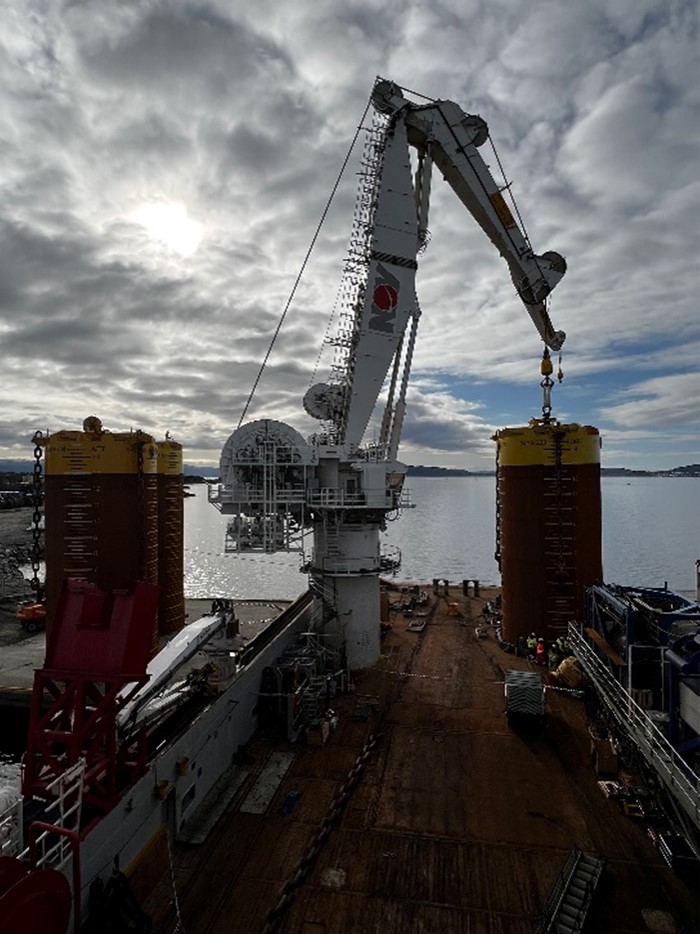
Loading suction anchor
After loadout, the vessel sets sail to the field. Transit to Tampen typically takes 9-10 hours and it is a good time to do final preparations. It is always nice when the vessel arrives at the field and is positioned with an orientation minimizing the impact of the waves (head sea). People onboard perk up – prepared for the operations.
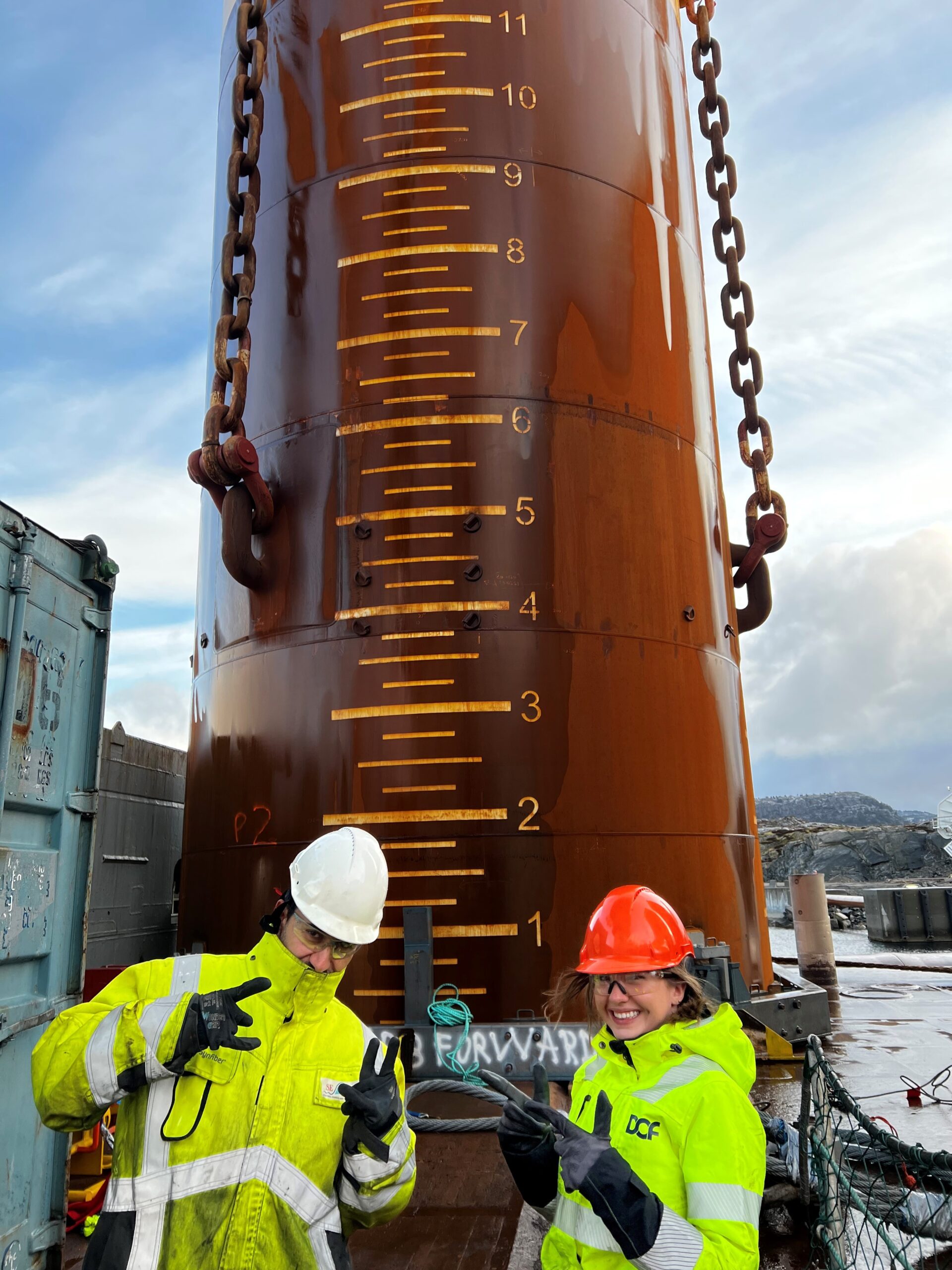
Project Engineers in front of suction anchor – Left: Izzet Salim (SEMAR), Right: Sara Marie Kjelby (Dof Subsea)
It has been exciting to see anchors with steelweight more than 100-ton being lifted and overboarded from the vessel.
There are large forces in motion, and it is important that there are well prepared plans with analysis of the various steps. One of the most important analyses are calculation of theloads in the crane during overboarding. If the loads breach the limits of the crane they cause overloading alarms, in worst case damage to the crane and resulting in operational challenges.
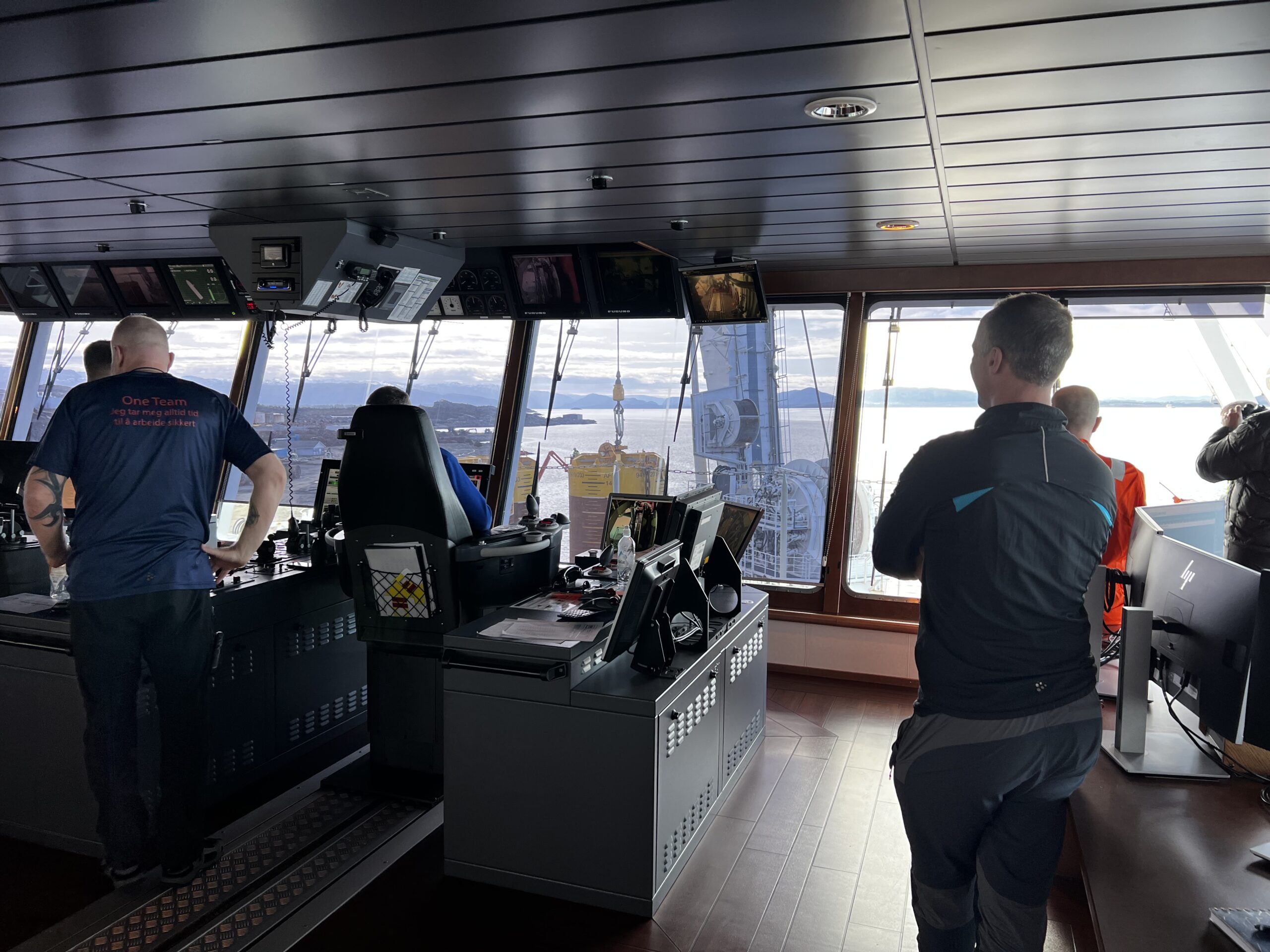
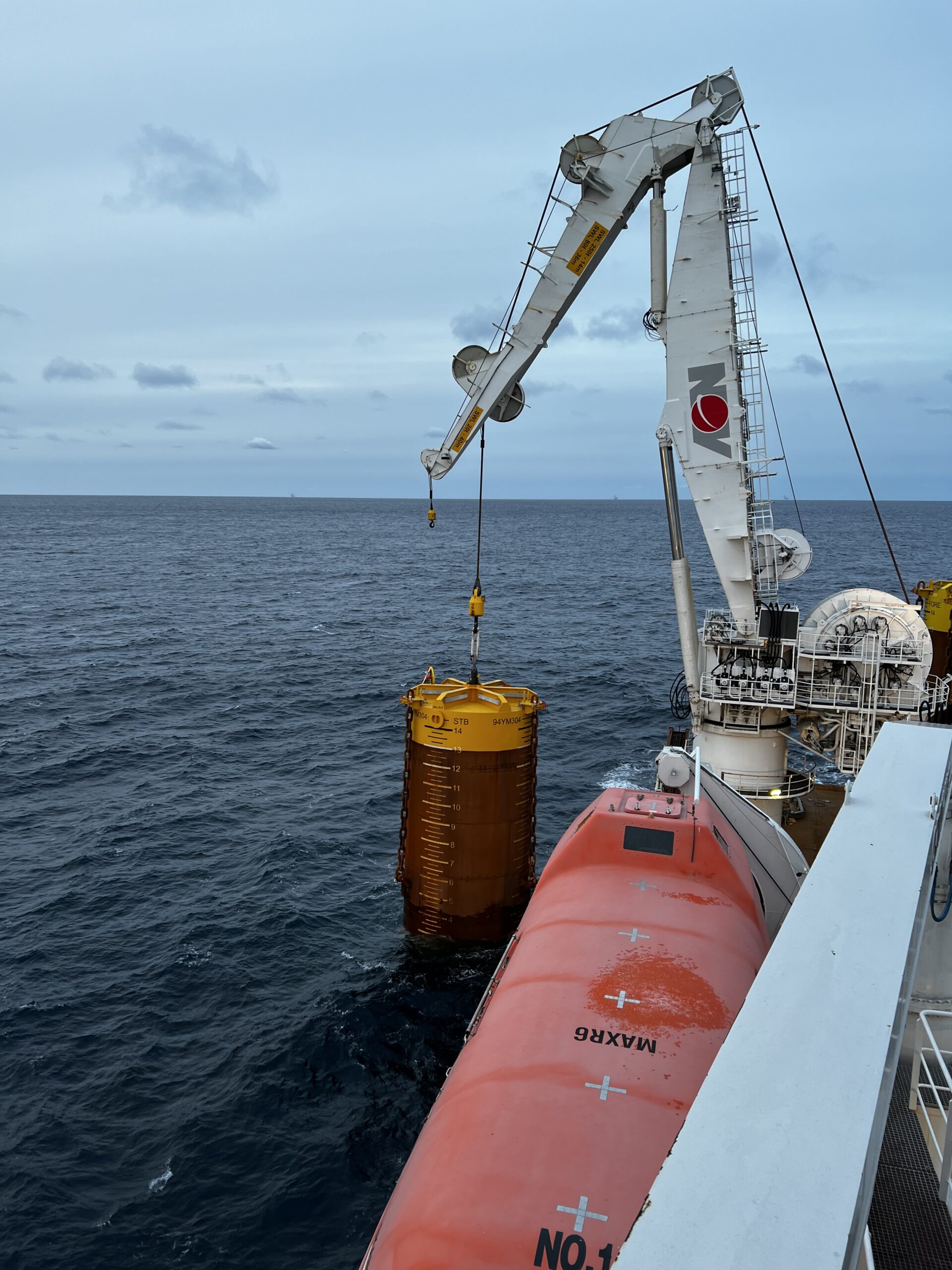
Suction anchor lift and overboarding.
Before going offshore, I thought that the most exciting part would be penetrating the anchor into the seabed. However, during this part of the operation there is very little happening above the sea surface.
The anchor is lowered into the seabed inch by inch over a period of several hours depending on the soil condition at the site. Water is pumped out of the anchor, which causes the anchor to be lowered into the soil due to low pressure inside the anchor.
The suction operation can be viewed through the footage from the Remotely Operated Vehicle (ROV). It can be interesting watching fish, shrimp and the arm of the ROV carrying out operations close to the seabed. However, since operations go day and night, this is also a nice and quiet time to sleep.
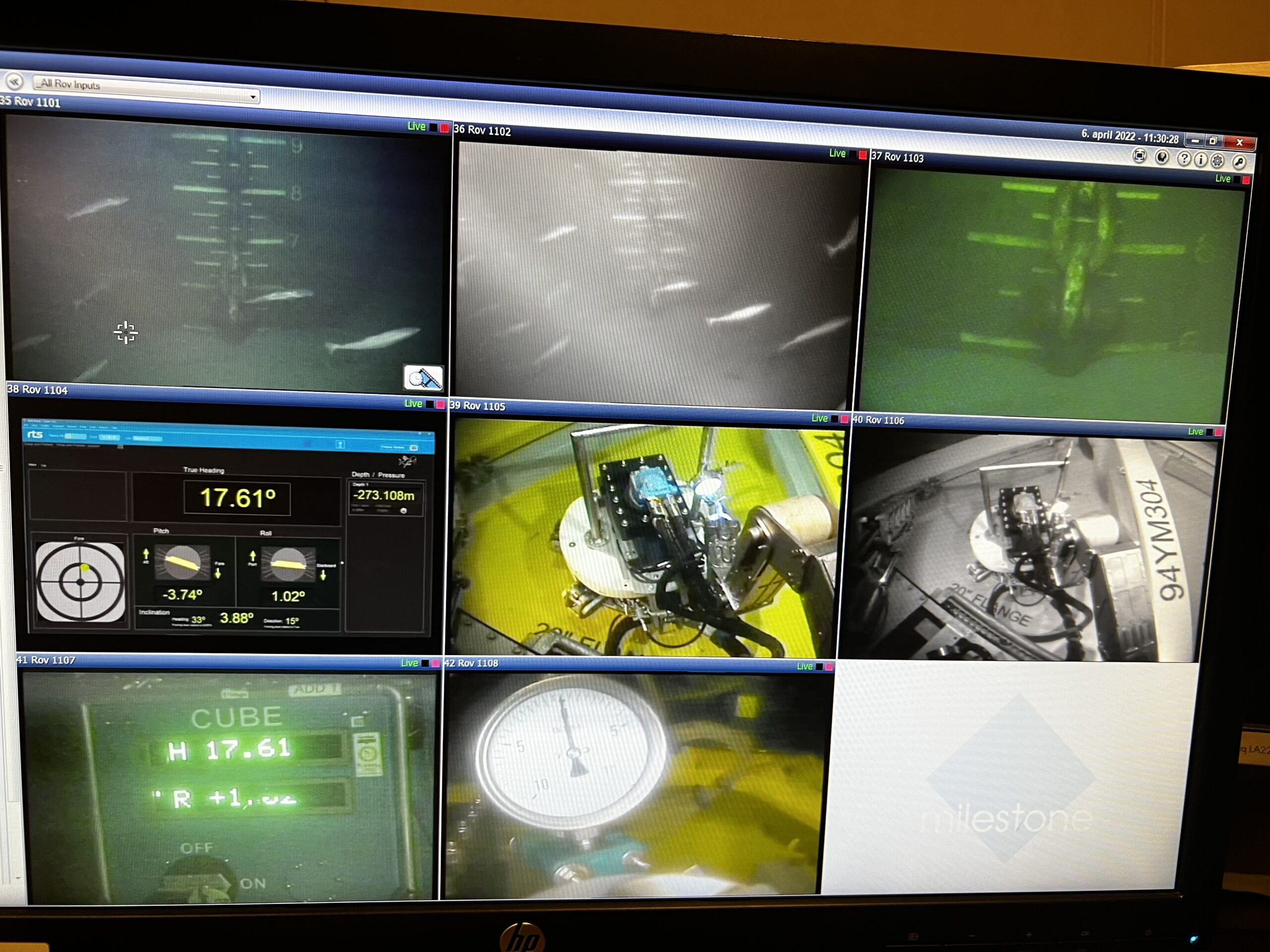
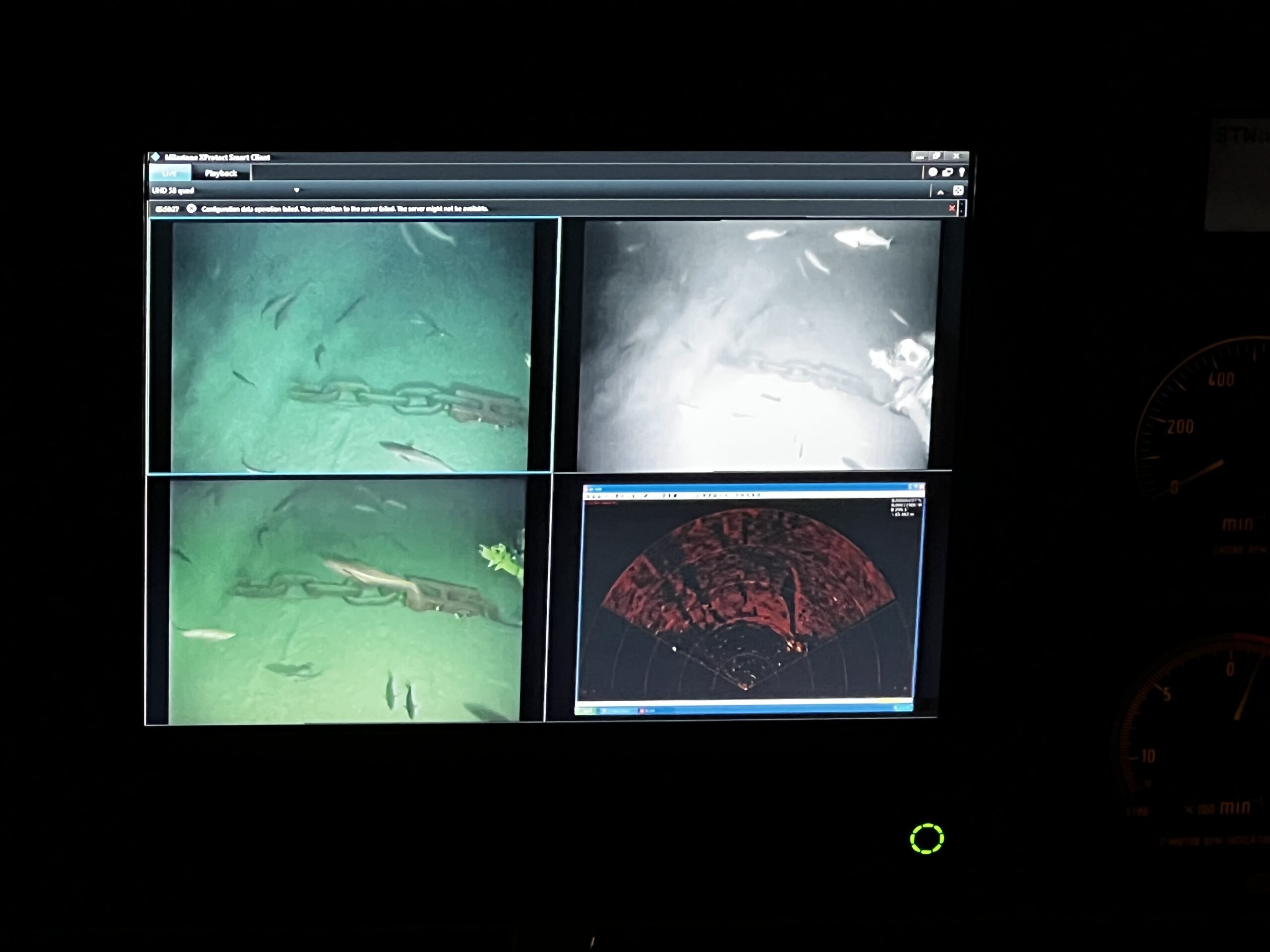
Remotely Operated Vehicle (ROV) operations on the suction anchor Fish close to the seabed
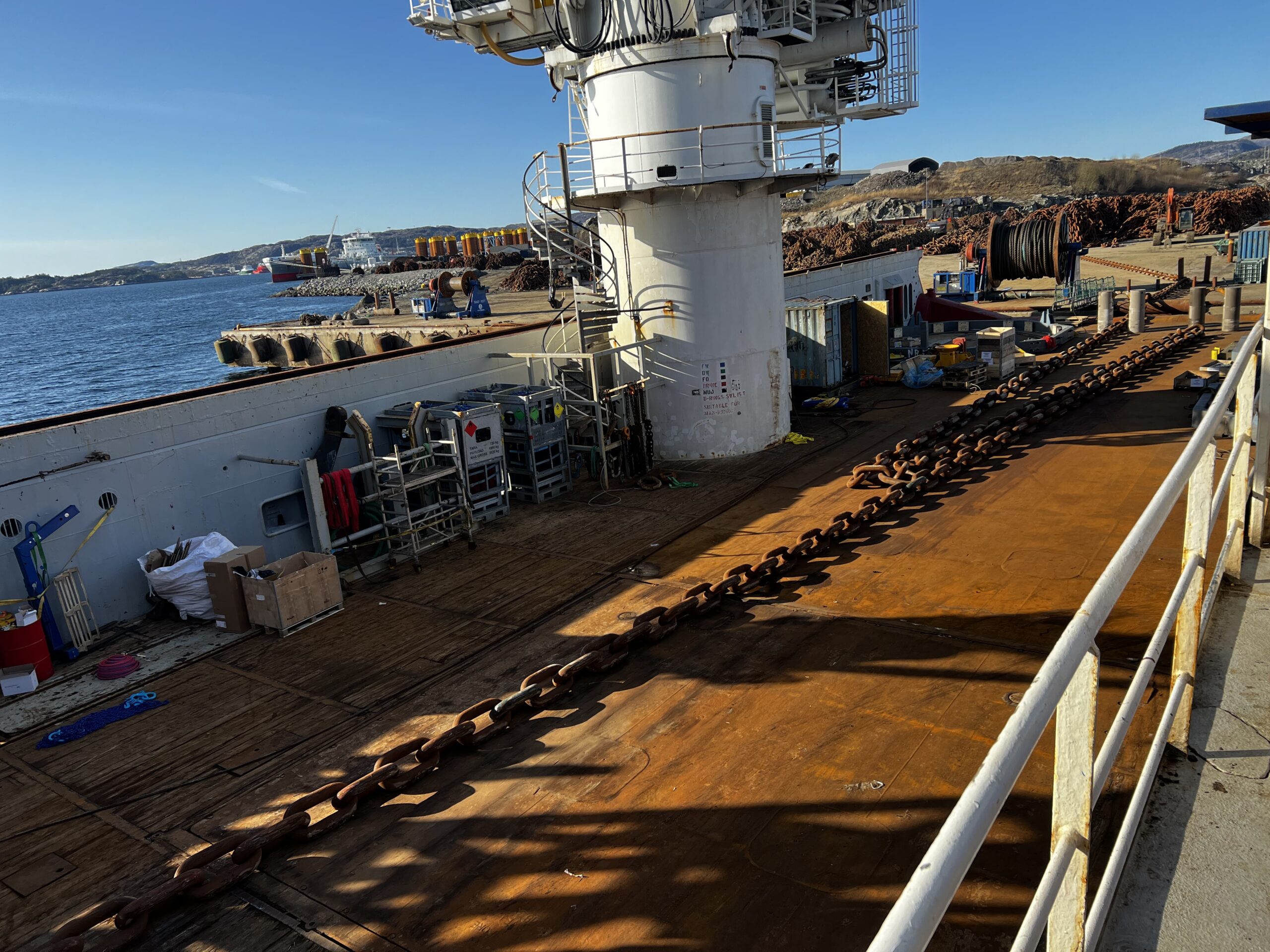
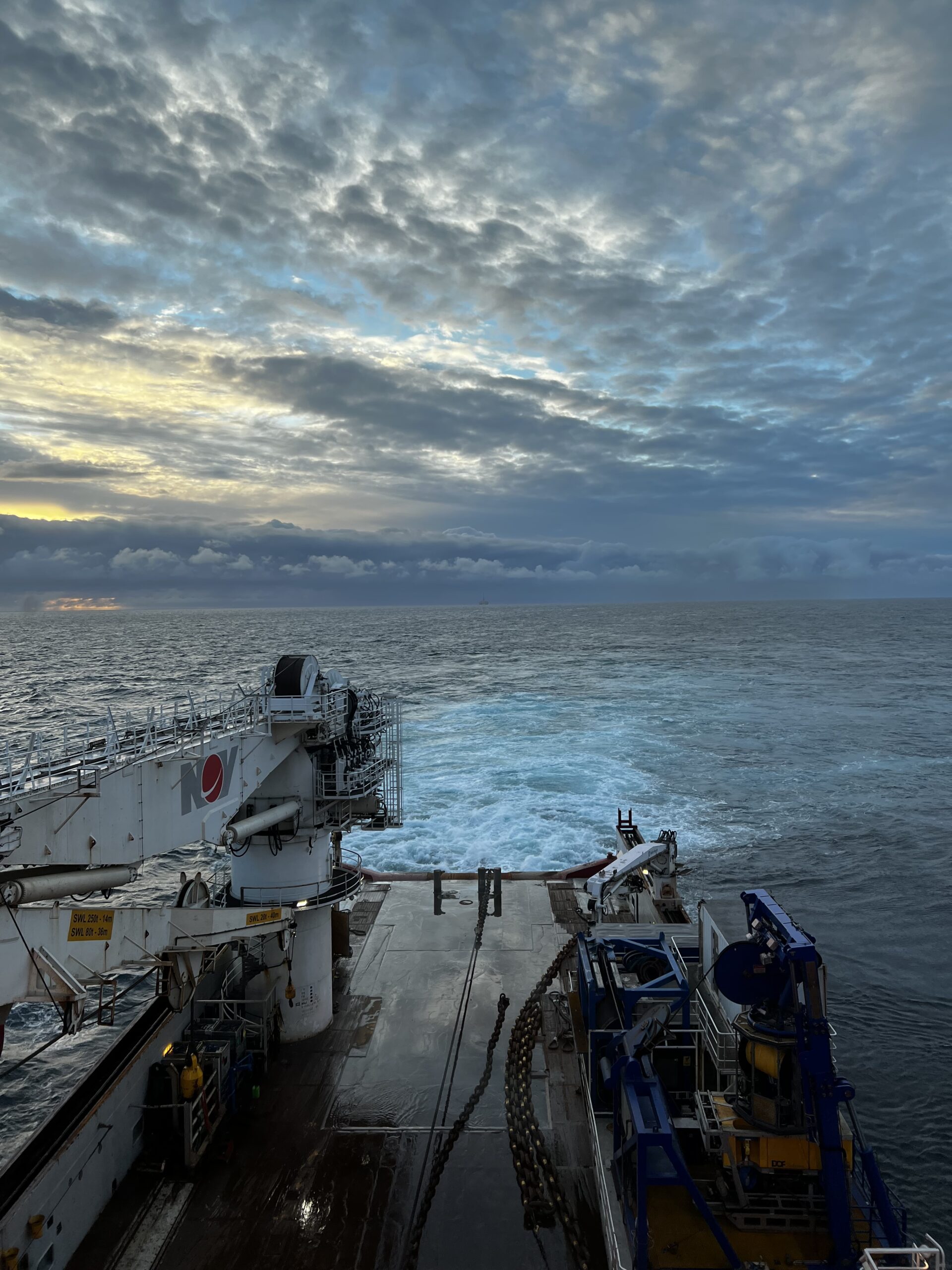
Bottom chain loading Tension test
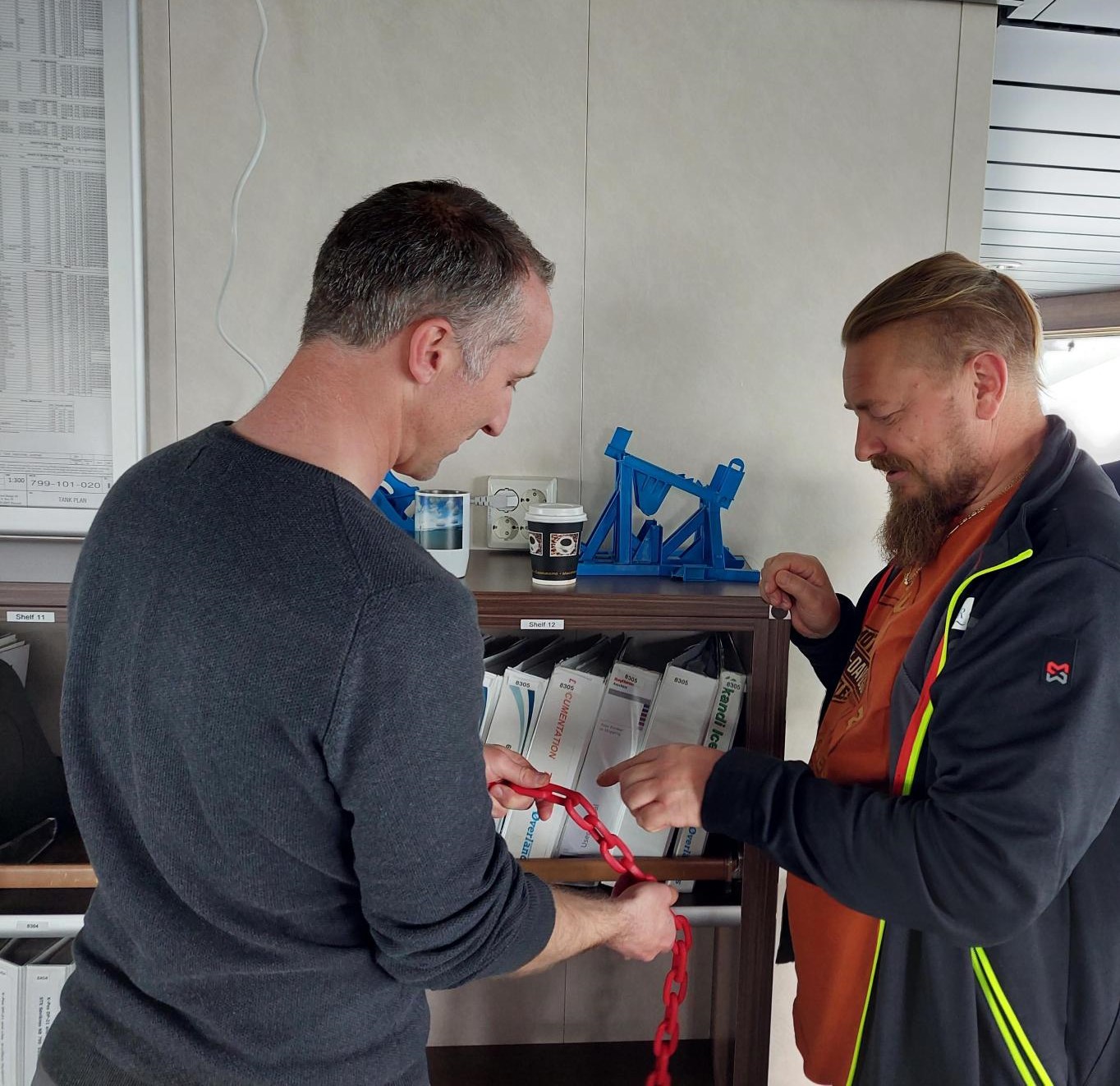
Evaluating twist in the chain
As part of the anchor installation campaign the bottom chain mooring segments are connected to the anchor which is installed on the seabed.
During the chain operations the boat vibrates. Large chains are dragged over deck and overboarded to start the spooling out of chain. After the chain is connection to the anchors, the chain undergoes a tension test where the vessel gives thrust so the load in the chain is about 300 ton for 30 minutes.
Luckily, the boats are designed to provide large loads. However, it was surprising to learn that the largest vibrations are due to the tunnel thrusters in the bow of the vessel, utilized to keep position during the operations.
Sleeping during chain operations could be a challenge but luckily most crew get used to the commotion.
Twist is a major topic when installing chain mooring lines and give the crew a headache. It occurs when the chain is laid with a certain number of rotations about its own axis. If the twist/rotation is left in the chain this can cause uneven load distribution on the chain elements and reduce the lifetime of the chain segments. It is confusing and takes a good amount of patience to pay attention to, and count, the number of rotations in a long chain segment. If twist occurs, a common method of removal is that the vessel takes a loop about its own axis. Small chain elements are kept in the vessels to help visualize the process and count the correct number of twists to remove from the chain.
The operations for all the 19 suction anchors of the Hywind Tampen project went smoothly. The engineering and planning were well prepared, and the crew onboard Skandi Skansen skilled. The anchor installation campaign is finalized, and we are currently underway in the “hook-up” campaign, where the floating wind turbines will be towed to site and connected to the installed anchors. It continues being educational and exciting being part of this adventure.
Recent Comments