If you ever get the opportunity to sail on an anchor handler vessel, it can be recommended to watch the sunset from Monkey Top (the deck on top of the bridge roof). Sitting on the top deck of a large vessel like Skandi Iceman travelling about the open sea is special; a strange type of break from everyday life for me, but life as usual for the crew.
Life onboard Iceman is surprisingly warm. Like the ecosystem below the surface, the one on board consists of a colorful collection of individuals who play their role in the bigger picture. For each of us the tasks of the others can seem like work of magic.
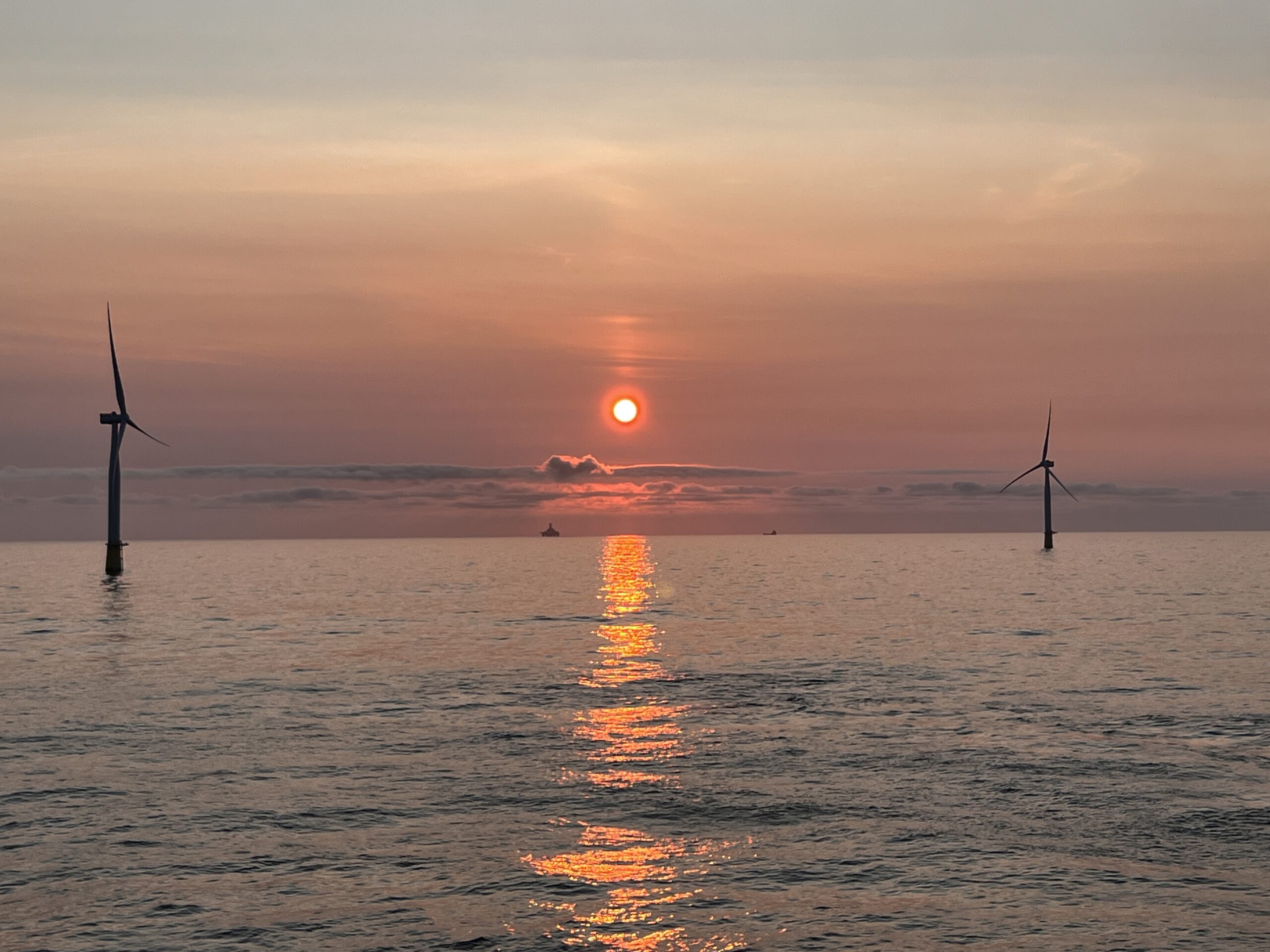
Sunset at Tampen
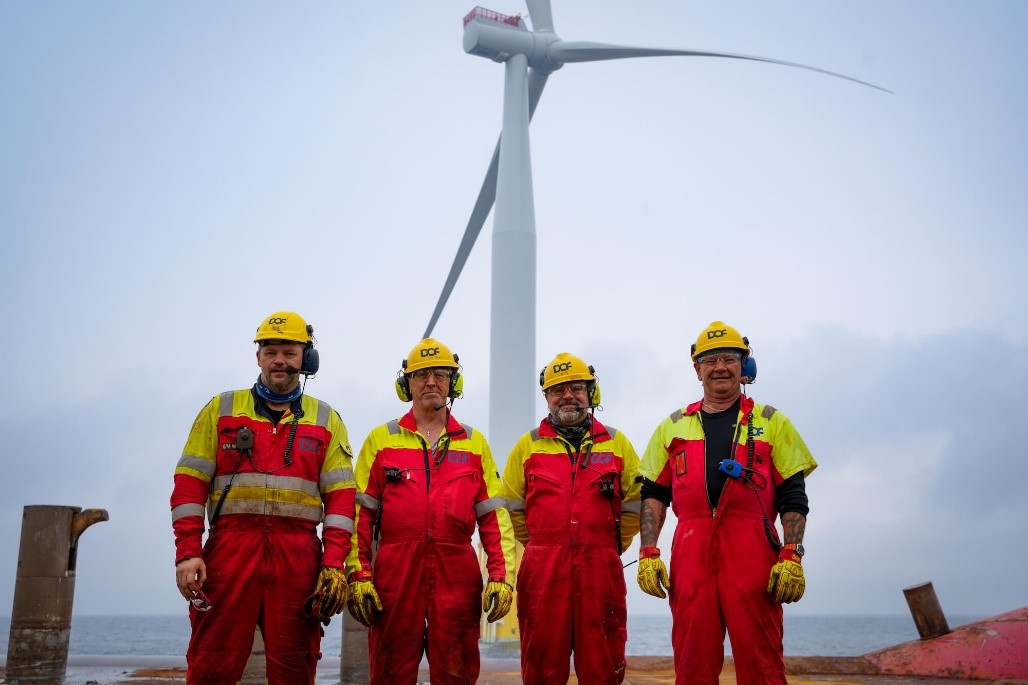
Skandi Iceman deck crew
Eleven floating wind turbines (FWT) are installed by DOF at Tampen site in the North Sea with vessel Skandi Iceman, in collaboration with SEMAR.
These Equinor wind turbines make up the largest floating wind turbine farm in the world, Hywind Tampen, with a combined effect of 88 MW.
The last phase of installation is the tow and hook-up campaign, where the floating wind turbines are towed to site and hooked up to the preinstalled anchors on the seabed.
Inshore
The first step of the tow and hook-up installation campaign is carried out inshore at Gulen, where the fully assembled wind turbines are temporarily moored in Fensfjorden.
Some components of the permanent offshore mooring are assembled inshore before tow-out, including sheathed spiral strand wires. These wires are spooled on and off the vessel winches, which are operated by the captain and officers from the bridge. They must be handled with care to prevent damage to the coating, bending of the wire or socket.
The deck crew connect the wires to preinstalled bridles on the floating wind turbine. Simultaneously, the captain and officers on the bridge keep track of the installation vessel position relative to the floating wind turbine, to prevent damage to the various mooring segments or other parts of the wind turbine. Prior to the offshore campaign Semar engineers carry out analysis to establish optimal positioning of the vessel relative to the floating wind turbine, considering design and equipment restrictions.
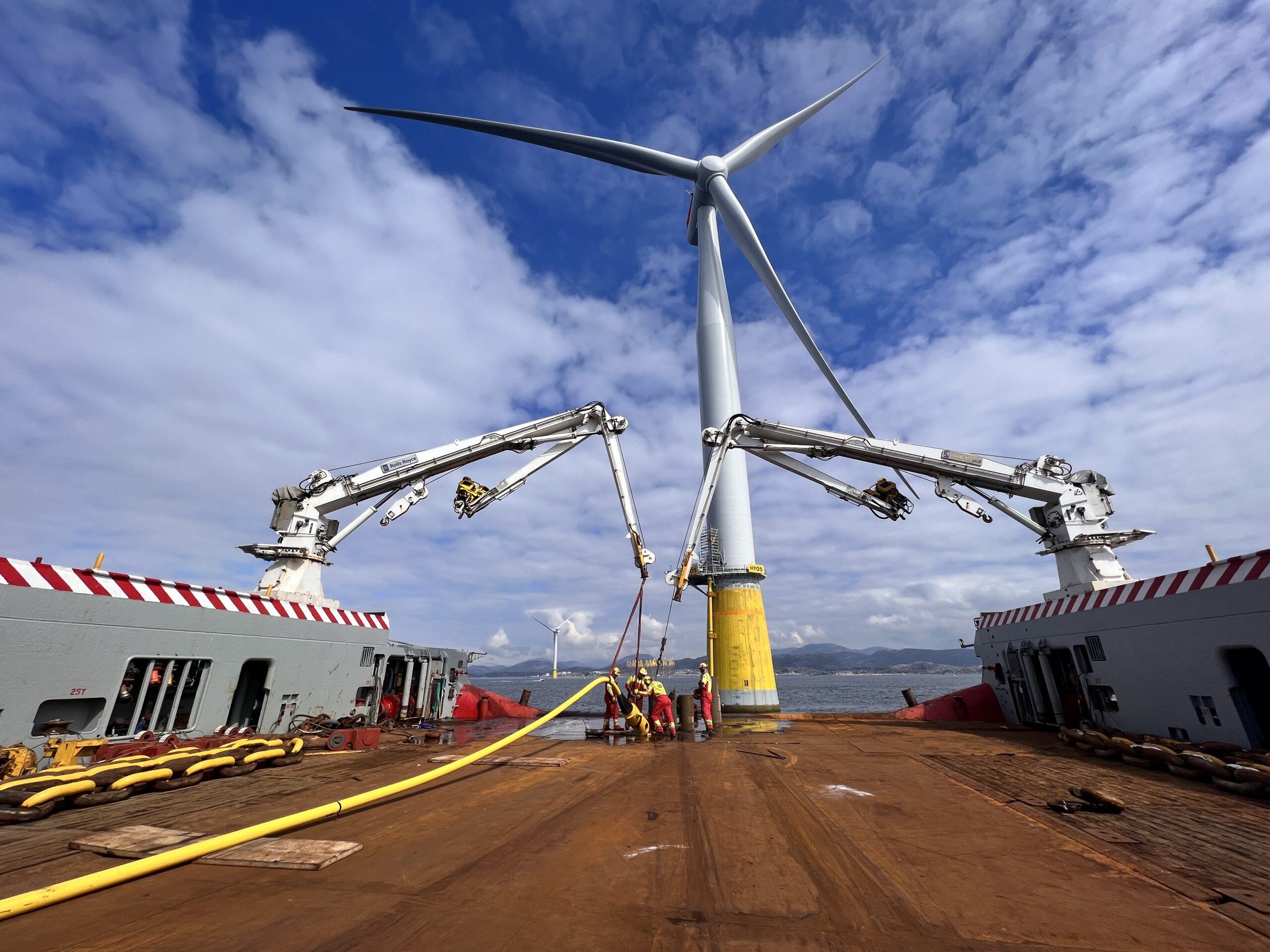
Connecting sheathed spiral strand wire (yellow) to wind turbine mooring segment
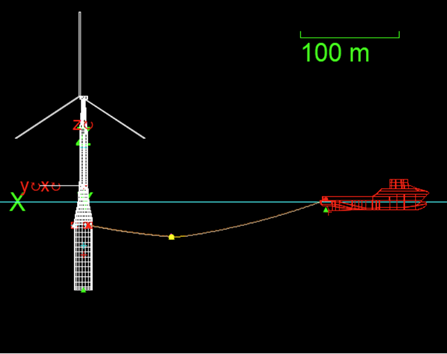
Orcaflex analysis of inshore operations
The sky was clear, and the fjord could be seen from its best side when towing wind turbine HY03. The tow-configuration for the Hywind Tampen project consists of one lead vessel (Skandi Iceman) with two trailing tugs. In addition, a fourth vessel is required for station keeping during mooring line assembly and hook-up at site.
The tow of a floating wind turbine is slow and steady. A trip to Tampen which typically is eight hours of transit, takes 36 hours with a trailing wind turbine. The captain, officers and towmaster make sure the turbine is transported safely to site. At tow speeds approximately 2.5 knots an interesting phenomenon was witnessed; the wind turbine had significant roll motion (turbine rotor side to side).
This effect may be resulting from a vortex shedding frequency of the flow at the upper submerged part of the substructure coinciding with the roll resonance frequency, causing vortex induced roll resonance. A slight reduction of tow velocity reduced the effect; however, this could be an interesting topic for further investigation.
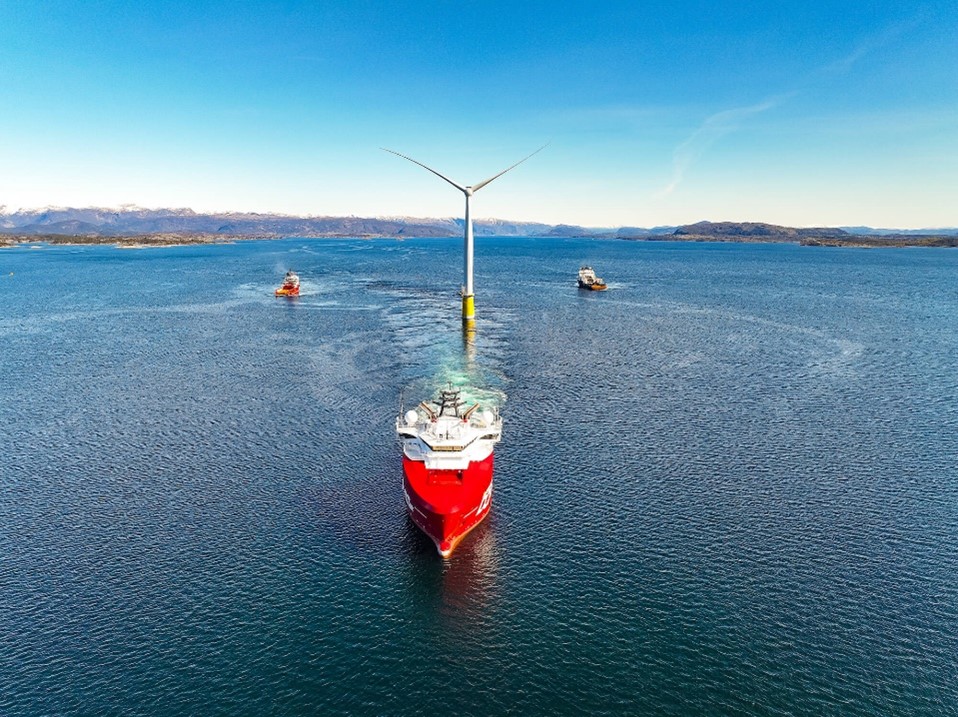
Tow of Hywind Tampen wind turbine with installation vessel Skandi Iceman as lead tug and BB Octopus and Island Vanguard as trailing tugs
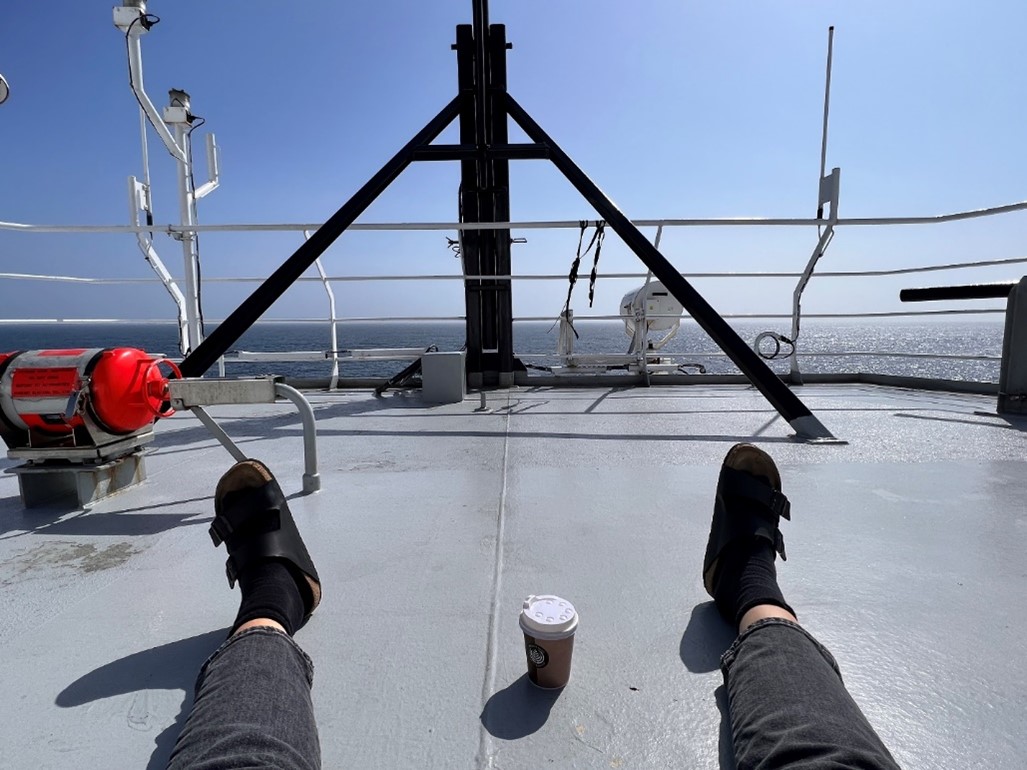
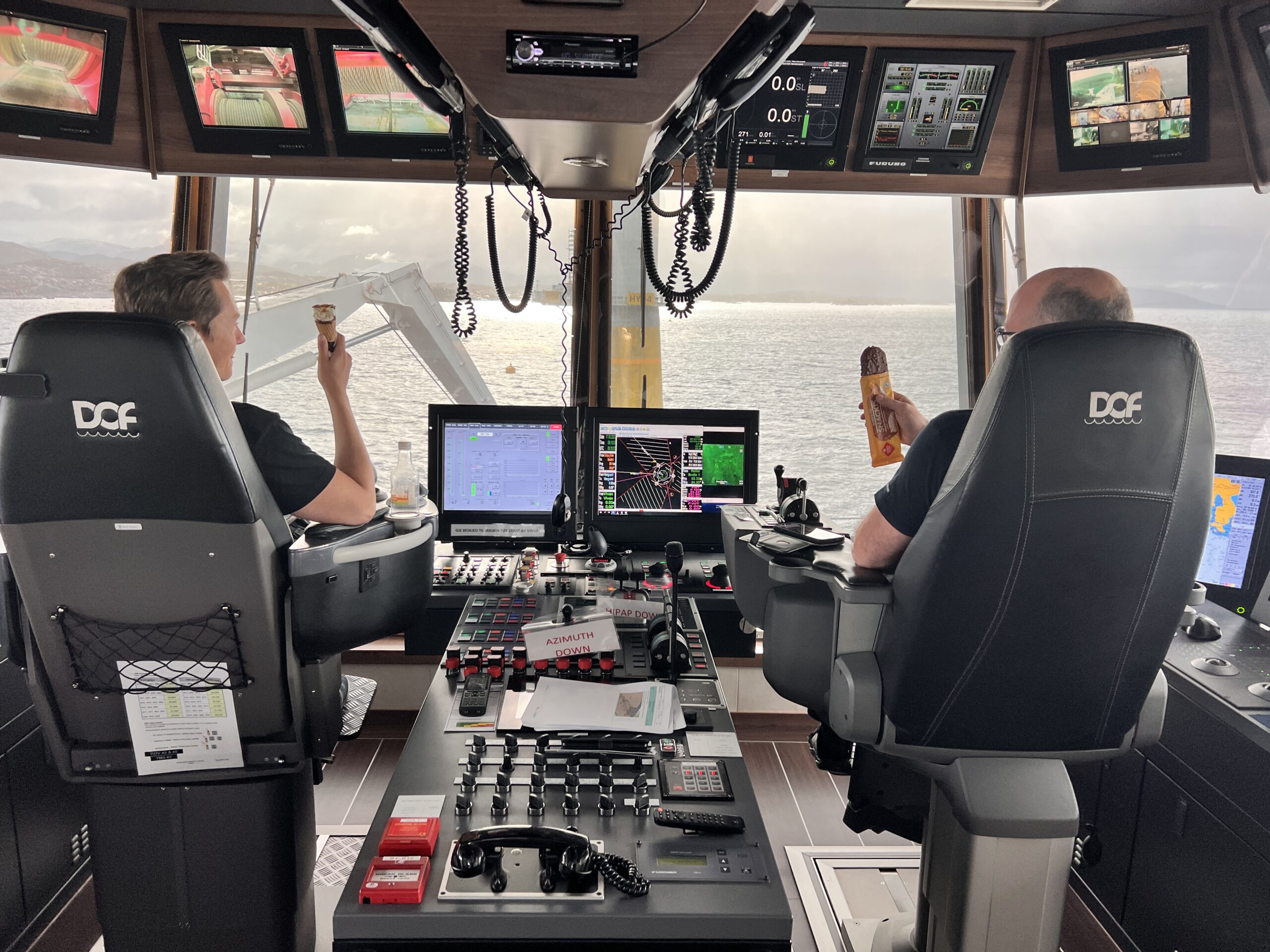
A cup of coffee on Monkey Top
Skippers eating ice-cream on 17th of May
Tow is a great time to be on Monkey Top, watch the view and contemplate. I was expecting to sail out in the open sea with nothing but ocean to see on the horizon, however there is a colony of humans and birds in the North Sea. Oil platforms and vessels can be seen. It’s a friendly place with beautiful sunsets and sunrises.
Now there are wind turbines in the mix. One blade of a Hywind Tampen wind turbine is 85 m which gives a total span of 167 m diameter rotor. It was not long since floating offshore wind turbines was a seemingly impossible task.
I am taking a moment on deck of Skandi Iceman to absorb this as a moment where a truly difficult task is being solved by a range of skilled people including scientists, engineers, various craftsmen of the industry and others. It is exciting to witness firsthand the collaboration it takes to carry out a complex project like Hywind Tampen.
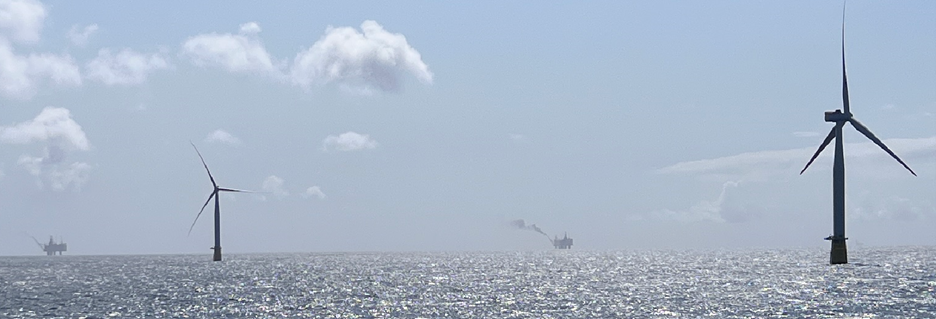
Hywind wind turbines and Gullfaks oil platforms at Tampen site
Station keeping
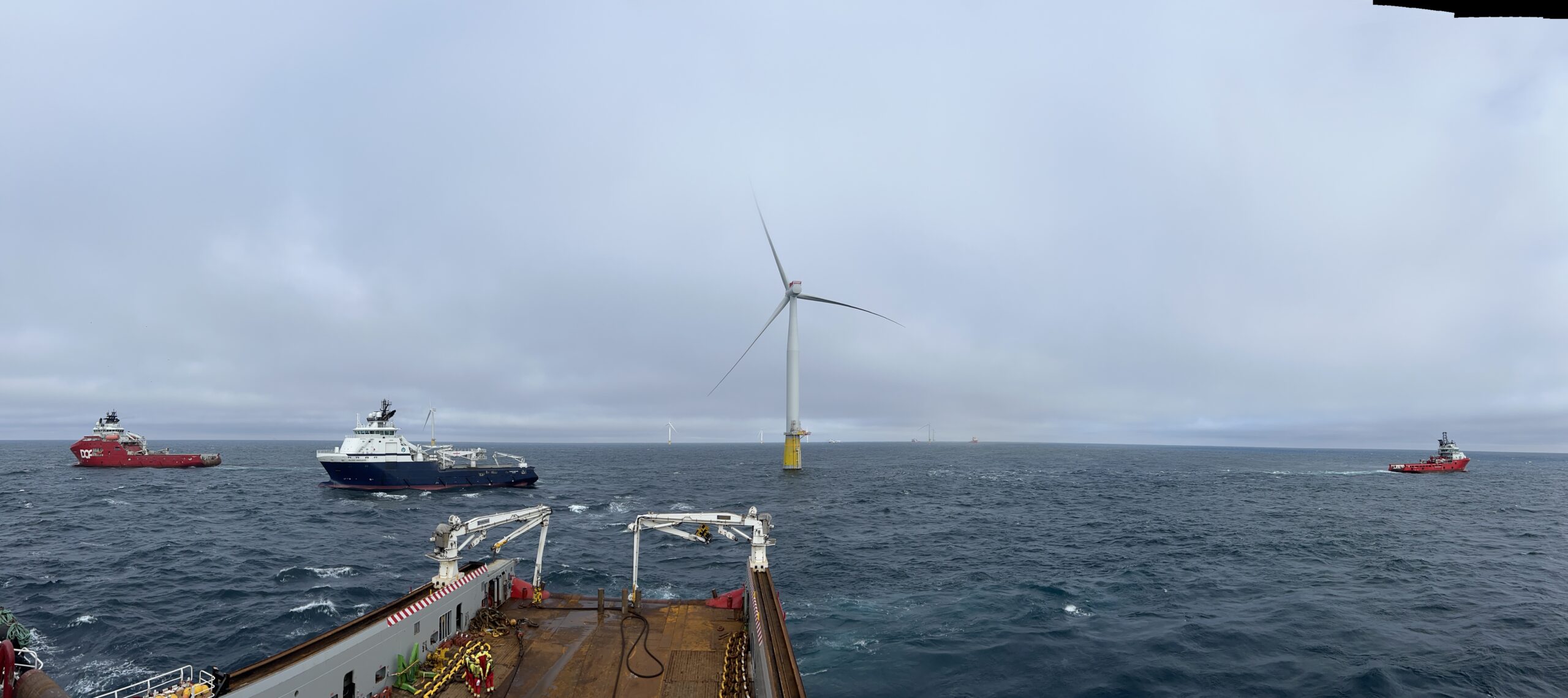
Station-keeping of FWT with three tugs/vessels
The first step upon arrival at Tampen is to carry out a 30-minute station-keeping test which is led by the towmaster. The towmaster’s role is to communicate with and organize positioning of all vessels and the wind turbine during operations. Over the VHF one can typically hear the towmaster communicating with the vessels, initiated by: “Octopus – towmaster”, and response from tug vessel Octopus: “towmaster – Octopus”, indicating that the towmaster wants to get in touch with the crew onboard Octopus and that Octopus bridge crew are listening.
The message for Octopus will contain updated vessel coordinates, heading and winch/tow line tension for station keeping activities, which is decided based on preestablished criteria for the operations, in addition to assessment of the environmental conditions. Towmasters are experienced as officers or captains and are familiar with vessel maneuvering. The criteria are set during the planning phase at the office prior to operations based on analysis and risk assessment by project engineers, marine consultants and clients, in collaboration with marine crew.
Hook-up
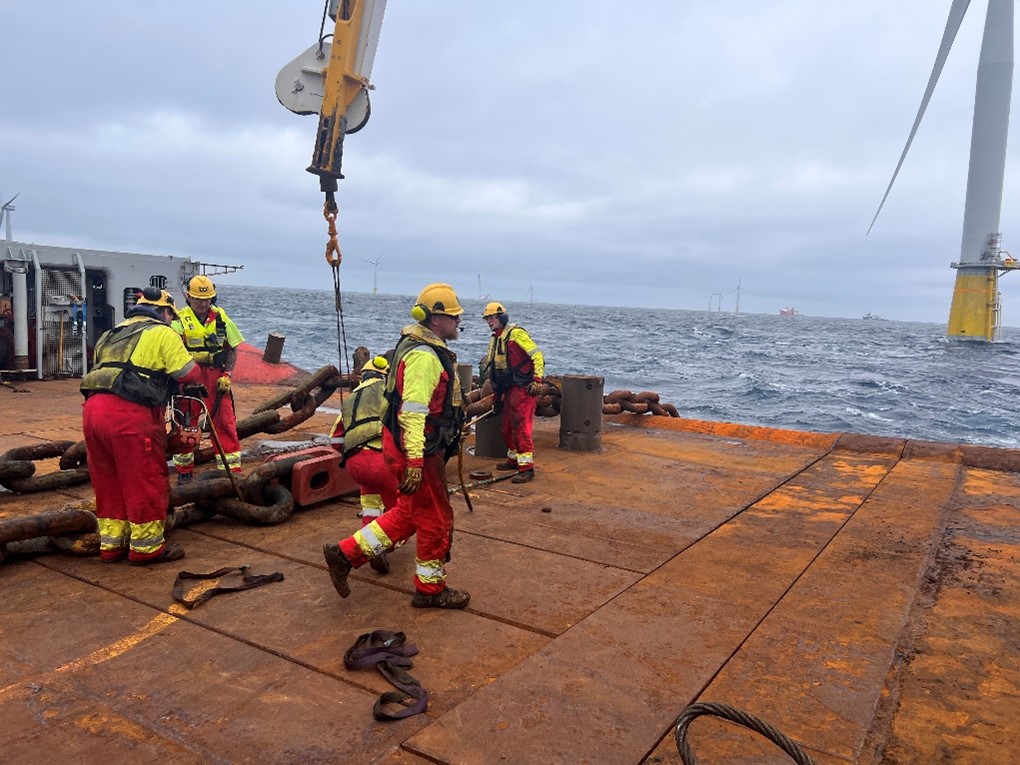
Deck crew connecting installed (inshore) mooring assembly yo preinstalled anchor and chain on seabed, as part of hook-up operation
Following successful station-keeping tests, concluding that the three tugs can hold the FWT in position, Skandi Iceman is utilized to connect the three installed (inshore) mooring line segments to the preinstalled anchors and chain on the seabed. Luckily, the chains are robust because a lot of heavy handling is performed by the deck crew to connect the various components.
It is fascinating to see how the deck crew on Iceman carry out tasks like well-oiled machinery. They are prepared for tasks several steps ahead and often without having to explicitly communicate they help and complement each other in tasks.
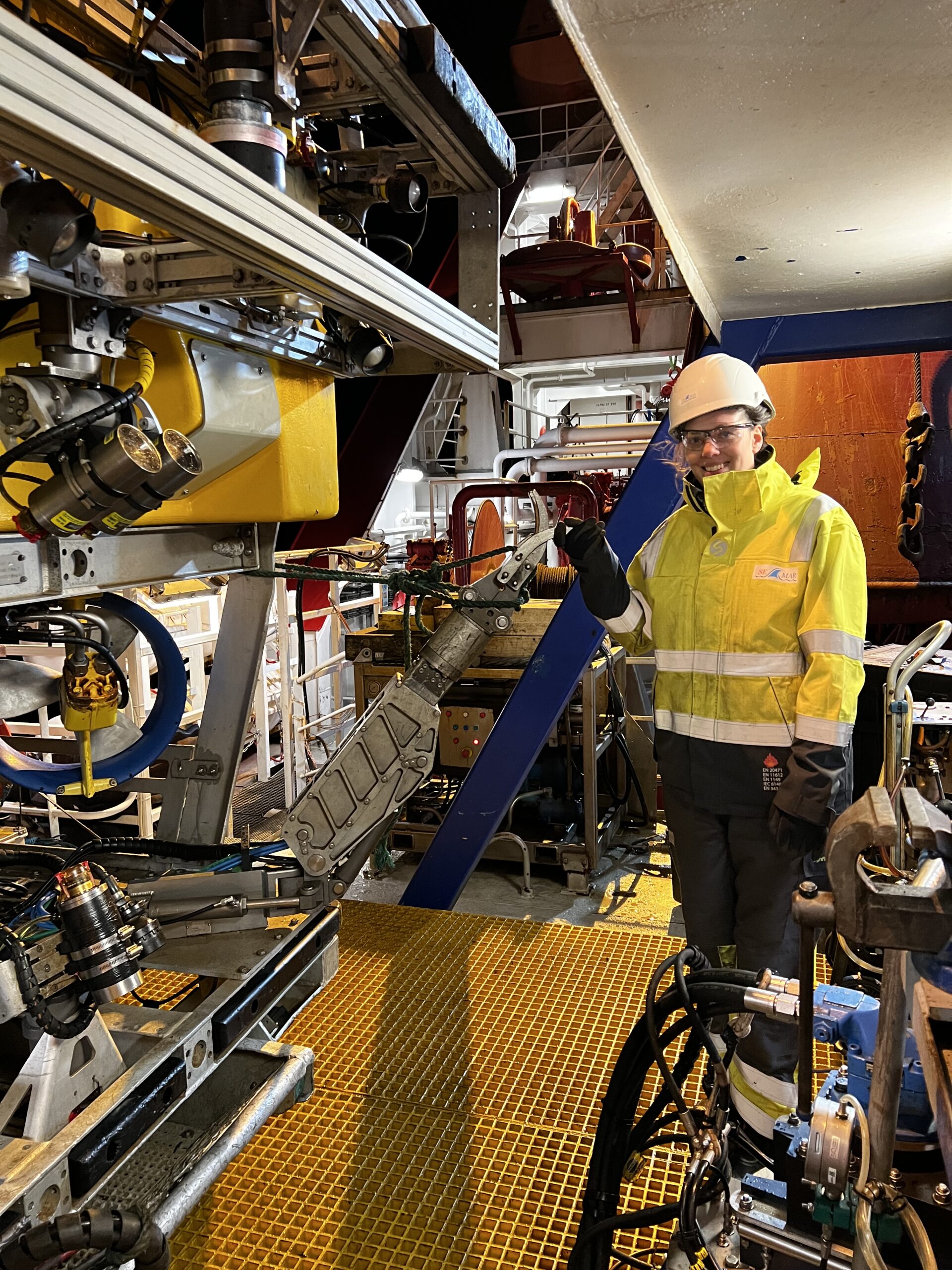
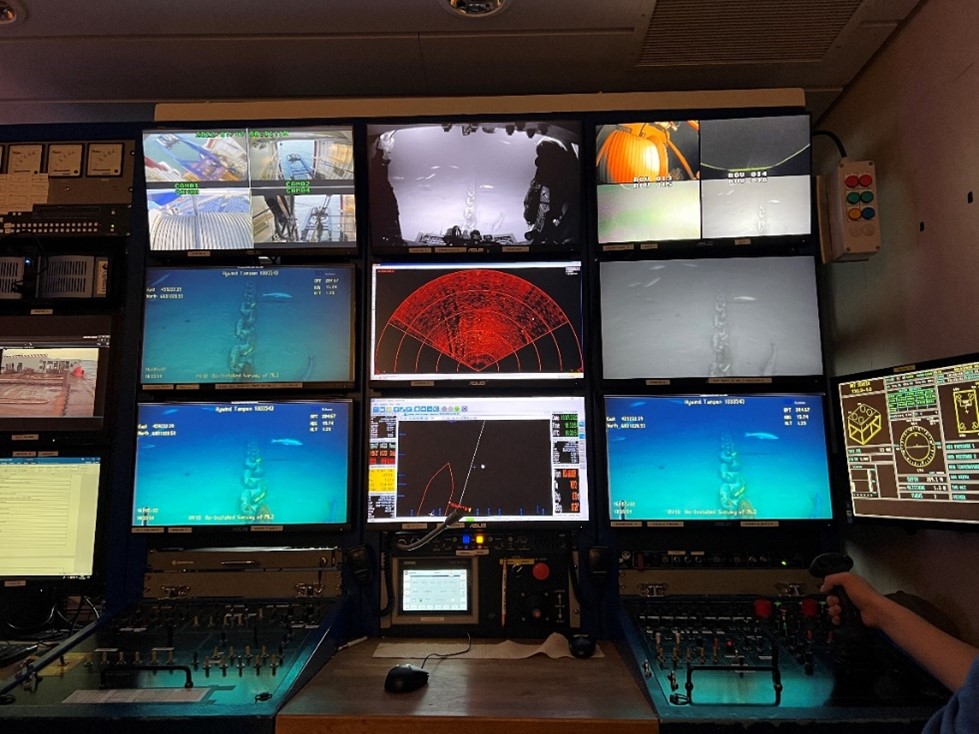
Project engineer greeting remotely operated vehicle (ROV) in hangar/vessel deck
Twist survey with remotely operated vehicle (ROV)
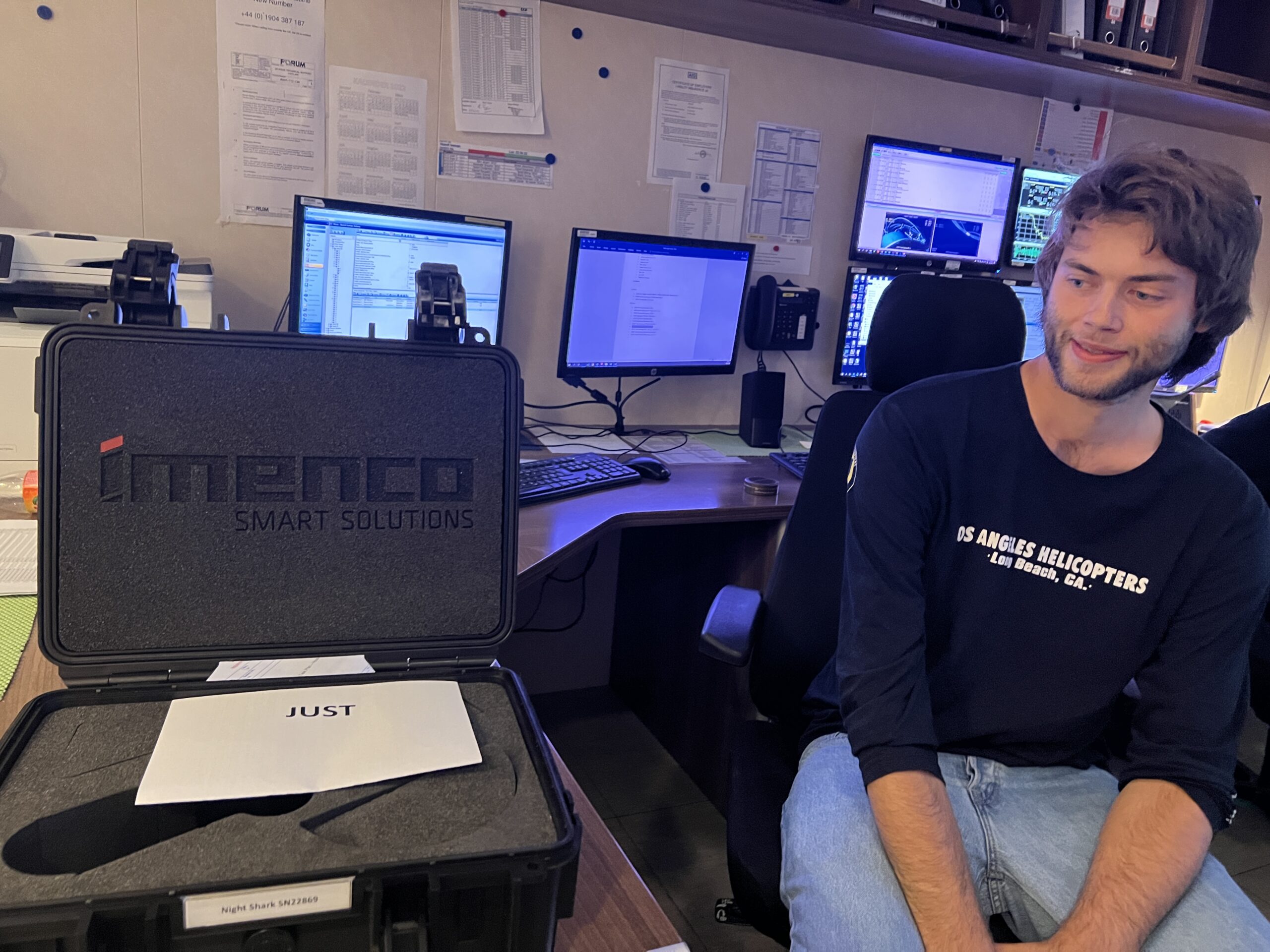
Just in case. ROV crew passing time and making puns while waiting on weather
The ROV crew fly remotely operated vehicles (ROVs) and are a humorous bunch who make lengthy and reoccurring twist surveys a breeze. Twist occurs when the mooring line is rotated a certain number of times around its own axis. If the twist/rotation is left in the chain this can cause undesirable load distribution on the chain elements and reduce the lifetime of the chain segments.
Throughout the twist surveys the ROV crew fly the ROV slowly over and film the entire length of the mooring (about 1 km per line) to make out the number of twists. Counting twists in mooring lines requires focus and is not as easy as one would think. Discussions can occur between project engineers, tow master, offshore manager, captain, officers and ROV crew regarding how many twists are in the line after surveys.
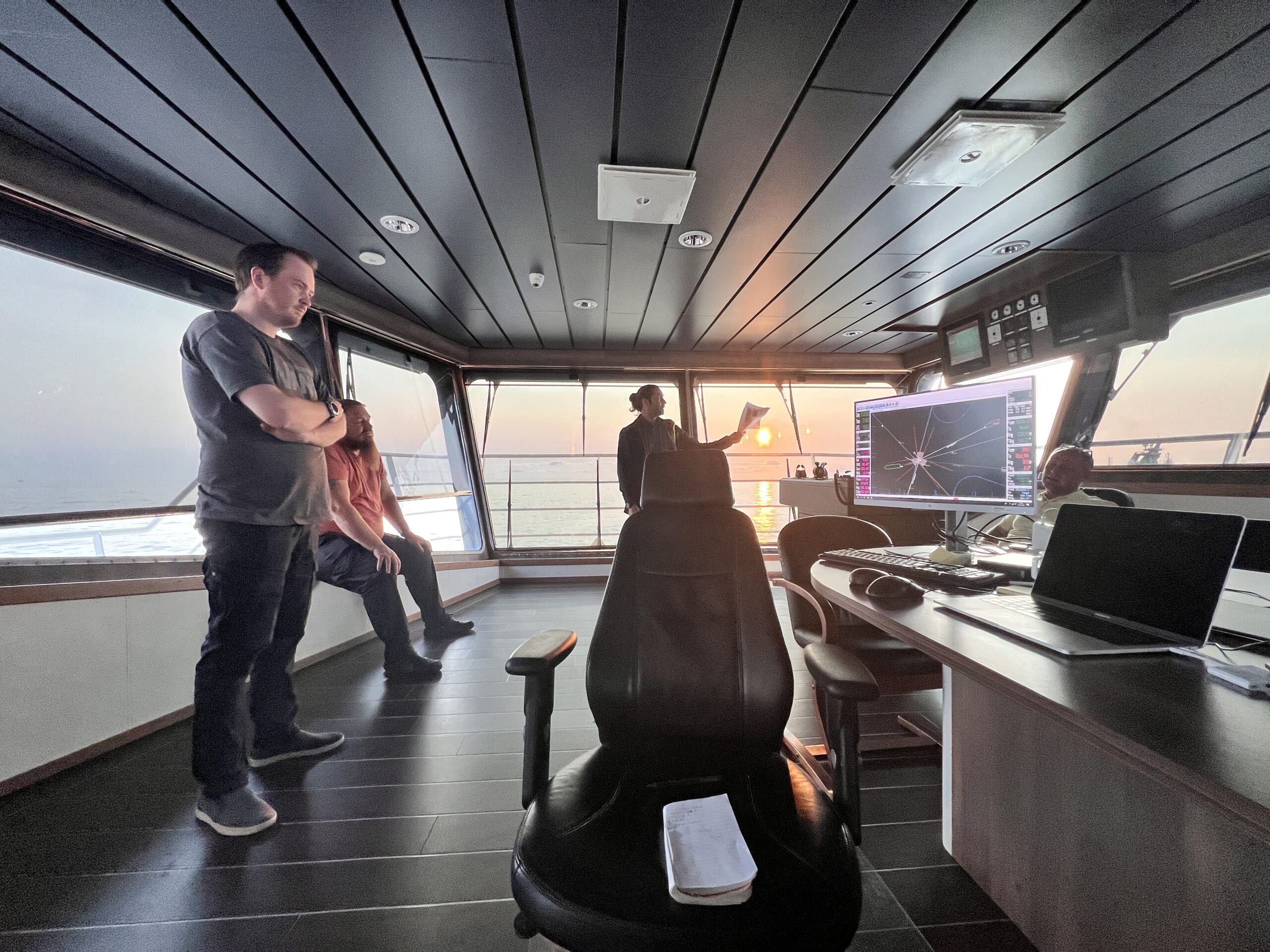
Twist discussion at the bridge with lovely sunset
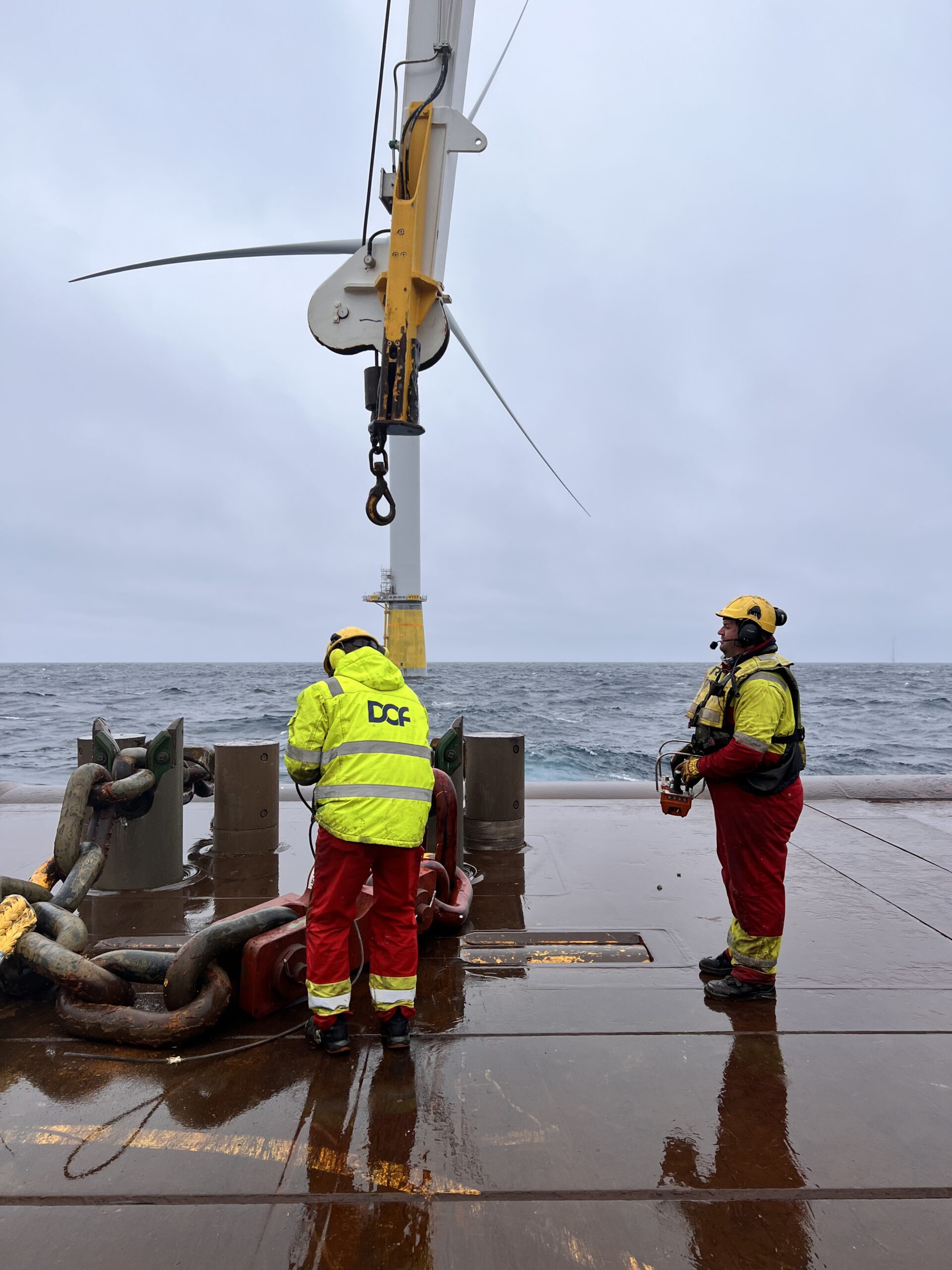
Hook-up of line on deck
If there are twists in the line during hook-up, the deck crew will counteract it by rotating the chains a similar number of times in the opposite direction on deck before final connection of the two line segments. Once they start twisting the chain it is near impossible to count twists in the chain, but the experienced crew know how to handle this conundrum and introduce the correct number of twists.
Inline tensioner (ILT) and tensioning
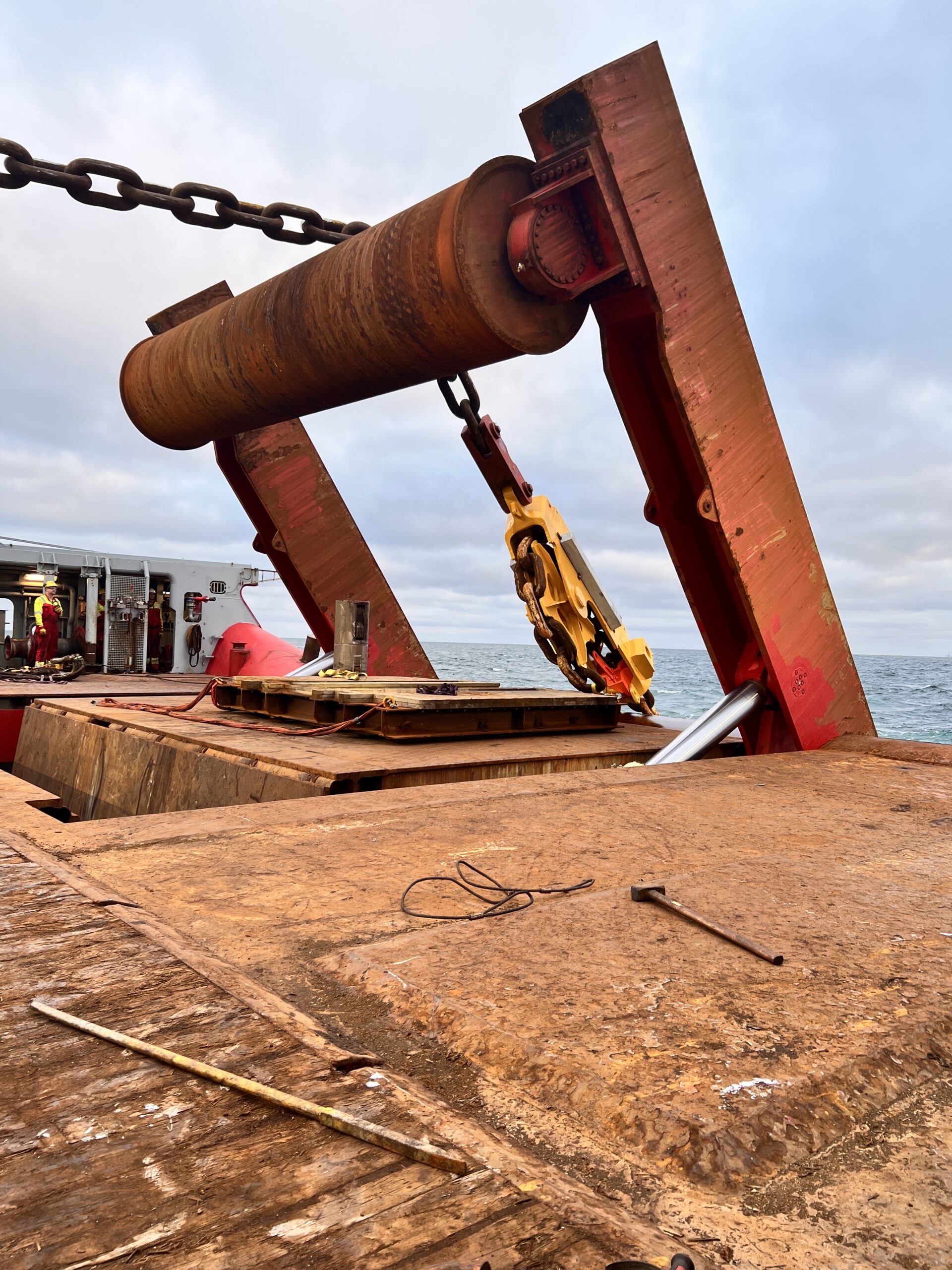
Overboarding of inline tensioner (ILT) with anchor handler frame (AHF). ILT skidding frame designed by SEMAR engineers
The final step of the installation campaign is tensioning of the mooring system with the inline tensioner (ILT). The ILT is a component of one of the three mooring lines, which is added to obtain the correct pre-tension in the moorings.
The vessels anchor handler frame (AHF) comes in handy for installation of the ILT. As part of the mooring line assembly, the ILT is connected to the installed mooring assembly and overboarded over stern roller (aft most part of vessel).
Use of the AHF frame prevents undesirable loading on the ILT by elevating it and eliminating contact with the stern roller. These boats are cool! The line is tensioned by pulling a chain segment of the permanent mooring line though the ILT, which is locked when the desirable pre-tension in the mooring system is reached.
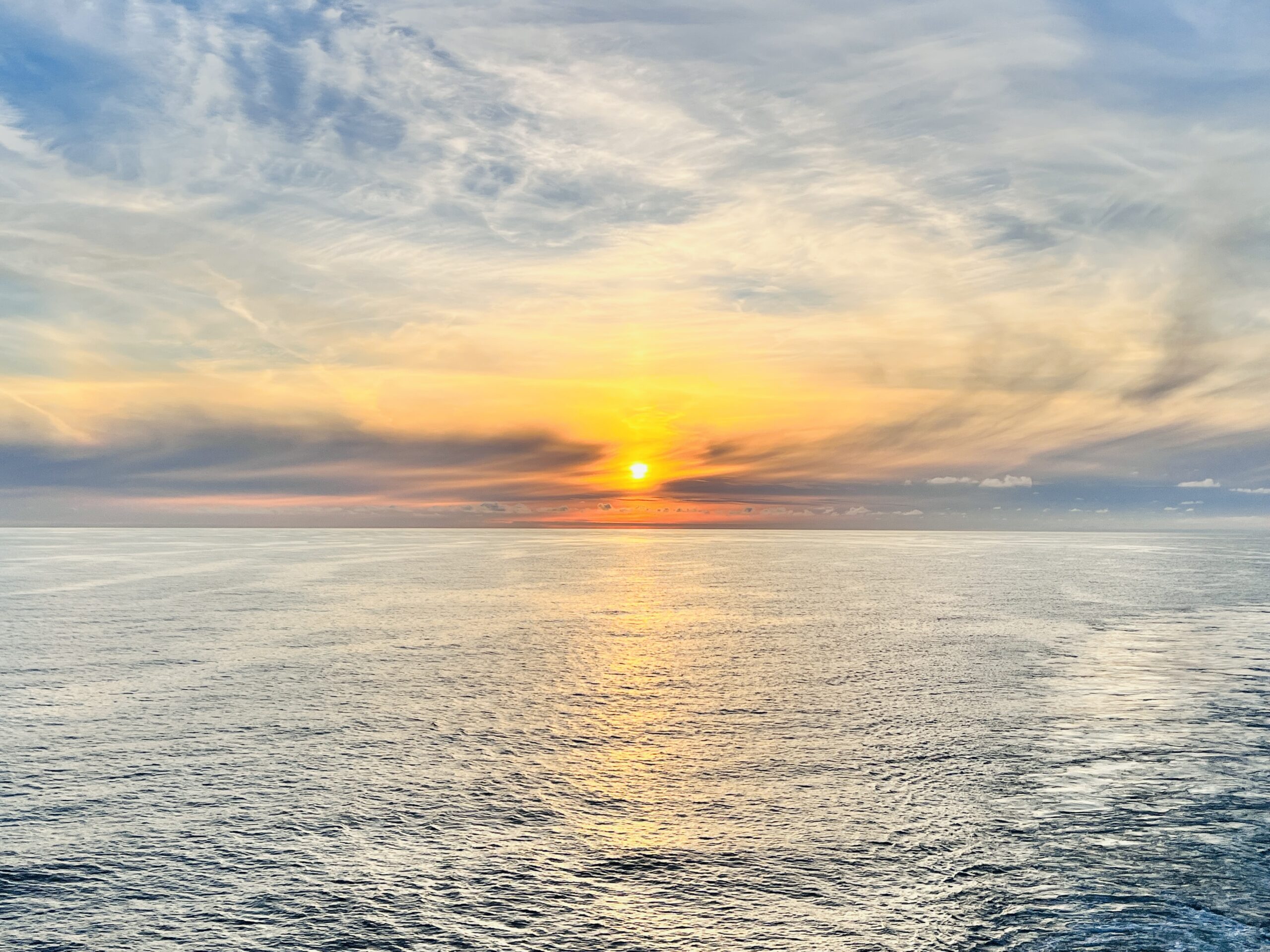
Sunset at Tampen
We are leaving soon. Tampen has gone from an area with a few platforms to a populated mix of turbines, platforms and vessels.
When the crew on Skandi Iceman releases the final connected mooring, the offset of the turbine from target position is within a 2 m radius, which gives us feedback that our calculations are appropriately accurate. Using algorithms to install wind turbines that withstand ravages of time and the wrath of the seas is a fun and challenging task.
Recent Comments