Experience in the oil and gas industry means we are used to one-of installations with tailor-made designs. Setting up floating wind farms with multiple identical units requires a different mindset to become feasible and economically viable.
We firmly believe that simplification and standardization of components and installation methods will be a crucial enabler for the floating wind industry regarding mooring systems. Traditional mooring systems rely on precise and high pretension levels, making mooring design, installation, and logistics complex.
Unique insights from Hywind Tampen
Today each mooring line in a floating wind farm has a unique line length as the water depth will always vary. Furthermore, each mooring line consists of components that have weight and high tension-induced handling requirements.
At this time, few professionals have experienced installing a complete offshore wind farm because they are few and far between. Being heavily involved in The Hywind Tampen project has given Semar unique insights into the complexity involved in installing offshore wind farms.
We have learned what is required to make floating wind farms ready and scalable for the considerable growth we expect in demand for sustainable power sources. It is paramount to limit the use of coal and nuclear plants, and even on-shore wind and solar power plants. We consider these options to be far more environmentally problematic alternatives for the electrification ahead of us, than offshore wind.
Read more: How can you improve the safety of your marine operation crew when installing an offshore wind turbine?
Minimizes the need for reengineering
Seabed bathymetry (water depth) and soil conditions vary across the vast area of a floating wind farm. Furthermore, there will be even bigger variations between different wind farms. With traditional mooring systems, this implies significant reengineering to arrive at appropriate site-specific designs.
For example, using a conventional system with mooring lines anchored to the seabed, each mooring chain is cut in an exact link to achieve the right amount of pretension after hook-up of the mooring system. Moreover, an equally high level of precision ensures that the anchors are installed in the correct position.
Ultimately, this limits the amount of standardization possible. Thus, different variants of the traditional mooring systems are needed within the same wind farm to achieve the required pretension, meet offset requirements for power cables, and account for possible sea bed contact restrictions.
With Honeymooring, Semar is developing a scalable mooring solution for floating wind. By sharing anchored buoys instead of anchoring the lines at the seabed, the system is directly scalable over many water depths.
Minimizes the need for reengineering
Seabed bathymetry (water depth) and soil conditions vary across the vast area of a floating wind farm. Furthermore, there will be even bigger variations between different wind farms. With traditional mooring systems, this implies significant reengineering to arrive at appropriate site-specific designs.
For example, using a conventional system with mooring lines anchored to the seabed, each mooring chain is cut in an exact link to achieve the right amount of pretension after hook-up of the mooring system. Moreover, an equally high level of precision ensures that the anchors are installed in the correct position.
Ultimately, this limits the amount of standardization possible. Thus, different variants of the traditional mooring systems are needed within the same wind farm to achieve the required pretension, meet offset requirements for power cables, and account for possible sea bed contact restrictions.
With Honeymooring, Semar is developing a scalable mooring solution for floating wind. By sharing anchored buoys instead of anchoring the lines at the seabed, the system is directly scalable over many water depths.
The mooring solution is easily adjusted for different water depths
Honeymooring opens for a significantly increased level of standardization. It is possible to adjust the system to different water depths simply by changing the length of the vertical mooring line from anchor to buoy.
Installation procedures can also be simplified and standardized with a repeated “isotropic” honeycomb pattern between the floating wind turbines, mooring lines, and buoys combined with low pretension levels.
The consequences are:
1. All wind farm units are installed using a single recipe, and the same installation procedure can be used for different wind farms.
2. All buoys within the same wind farm and their subsystems, vertical tendons, and horizontal lines will be identical. This allows for standardized serial production of key mooring components.
3. Due to the low pretension, high flexibility, and light material, the mooring line components can be simplified, and the number of components per line is minimized. Additional tensioning equipment will not be required.
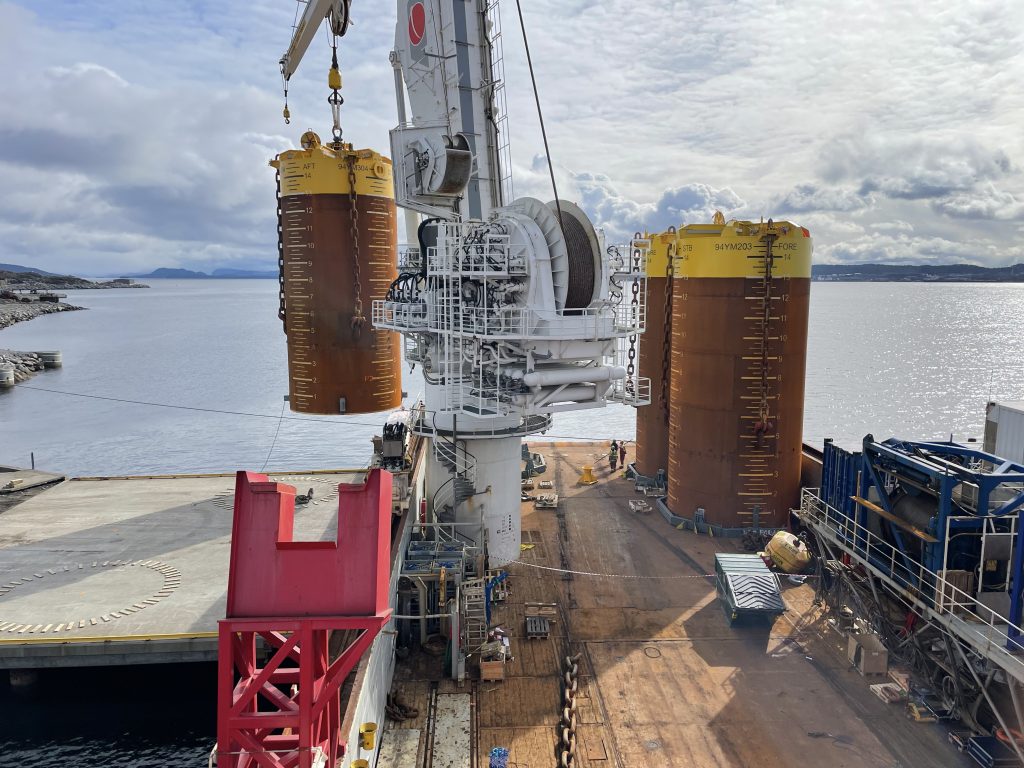
The mooring solution is floater agnostic
Various floating foundations for floating wind turbines have been proposed to minimize material cost, ease topside installation, and maximize performance.
Whether your floating substructure is a SPAR, a semisubmersible, or any other innovative floater design – as long as it is not a tension-leg platform, it is possible to moor with Honeymooring. In simpler terms: Honeymooring does not care about how your floater looks, it only cares about its fair lead position!
While being developed with the floating wind industry in mind, the system is applicable for any floating structure which will benefit from being moored in arrays. This includes aquaculture structures as well as floating solar parks.
The advantages of standardization
You can streamline the production process with standardized mooring components. Furthermore, it enables local production and thereby the potential to create jobs regionally, which will be an important criterion when governments award licenses to develop commercial projects.
Moreover, you can explicitly design standardized components for easy transportation and installation. This fact will significantly reduce the time needed for installation. Thus, the goal to install an entire floating wind farm in one year rather than several seasons is attainable. The fact that Honeymooring enables standardization can reduce the cost of mooring, including installation, enhance the efficiency of marine operations that can hasten “first electron,” and stimulate local industries.
This means quicker access to greener and more sustainable energy. You will spend less time analyzing, planning, producing, and installing the wind farm using Honeymooring. Standardization also increases scalability. The wind farm size can easily be adjusted, and the layout optimized.
Keeping it simple is vital for floating wind farms
With the increasing attention toward wind farms with floating units, the possibility of improving the efficiency of installation and marine operations is evident. With many identical units, even small gains in installation time for a single unit may contribute considerable benefits to the entire wind farm.
We believe that to achieve this, reducing the complexity of operations is the way to go. Honeymooring, with its possibility for increased standardization, addresses this by simplifying marine operations. We believe this will be a significant enabler for the success of the floating wind industry.