It is feasible to simultaneously improve crew safety and ease installation, maintenance, and repair of floating wind farms. We are bringing a new and innovative mooring solution to the table.
Installing an offshore wind turbine is time-consuming and demands extensive planning and attention to detail. Using traditional mooring methods involves heavy steel chains that are challenging to produce, transport, and install. The high pre-tension and high component weights mean high potential energy. This increases the possibility of severe accidents involving the installation crew or employees in production or transportation.
Labor and cost-intensive HSE-efforts
Heavy steel chains and chain components must be transported safely to and from the dock onto specialized vessels to the wind farm’s location. If an accident happens, the possibility of it having fatal consequences is proportional to the potential energy involved in the accident. Thus, planning for HSE and making the risk as low as possible demand a lot of time and resources in high-potential-energy operations.
The solution? We believe the answer to improving crew safety in mooring and marine operations is to migrate to lower component weights and lower pre-tension levels. We suggest mooring the turbines in a new and innovative way, called Honeymooring.
Reduced tension means reduced risk
With Honeymooring, the heavy steel chains are replaced with lightweight ropes organized in a honeycomb structure. The buoys are submerged and taut moored to the seabed. The turbines are moored using ropes connected to the shared taut-moored buoys. Using relatively horizontal mooring ropes instead of steel chains means reduced tension in the system.
We achieve lower pre-tension because of the reduced component weight and the more horizontal angle of the lines hooked onto the floating wind turbines. Furthermore, Honeymooring will enable power cables to be guided through the water column between the turbines, making cable-induced offset criteria less strict, which will ease the pre-tension requirement.
Increases the crew’s all-round safety
Crew safety is improved since the Honeymooring system has low pre-tension levels and primarily lightweight components. Reduced tension also makes the operations more straightforward and faster for the crew to carry out. Lighter lines are more manageable and easier to handle during transportation.
High tension operations increase the risk involved in deck operation due to the potential energy stored up in the system. Reducing the tension increases the crew’s safety onboard the vessels executing installation, heavy maintenance, and decommissioning.
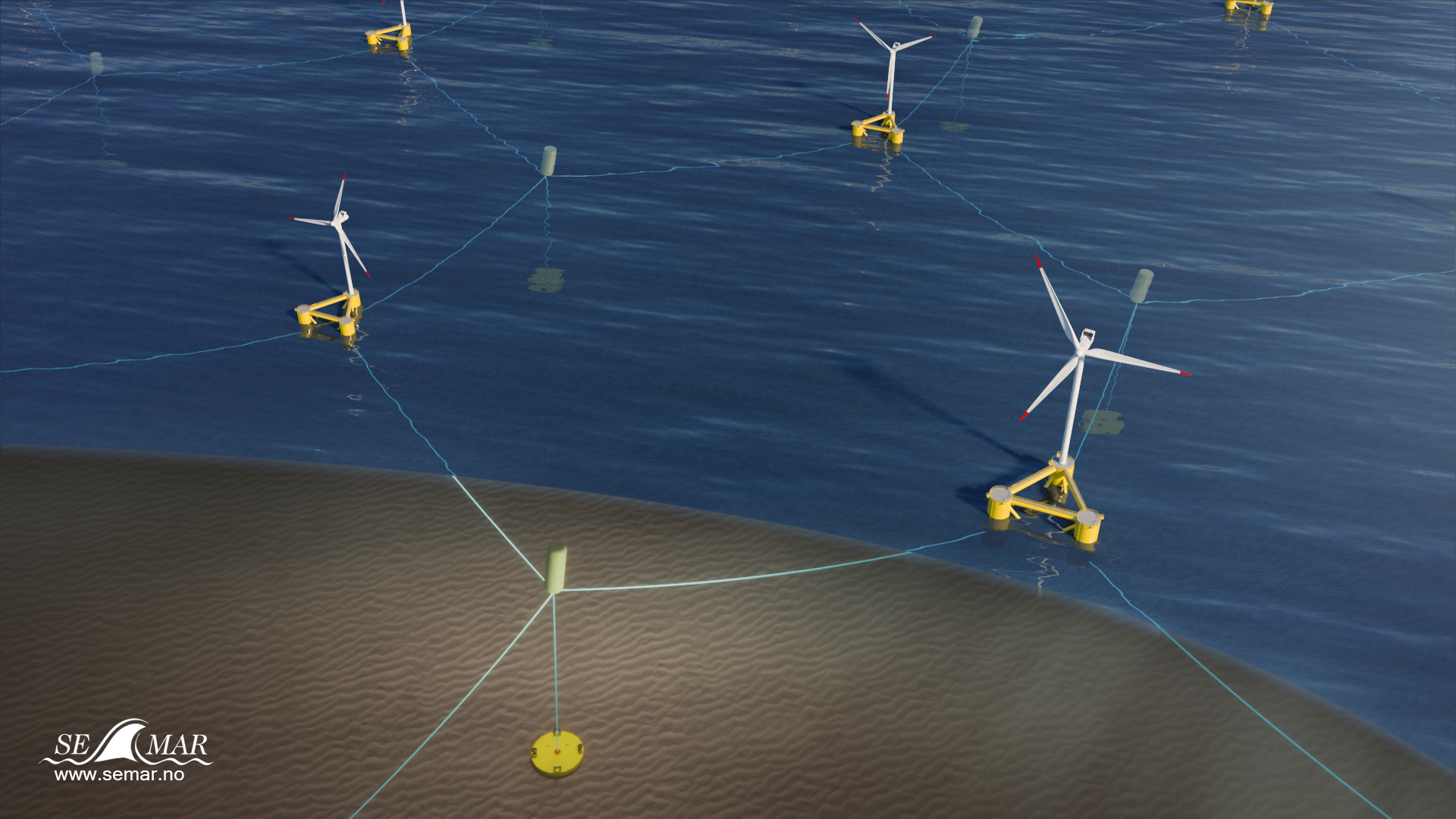
Huge gains are possible
The future floating offshore wind farms will consist of large numbers of entities instead of a single production platform for energy production.
With the rapid up-scaling of floating offshore wind farms, there is an urgent need for standardization, simplifications, increased scalability, and, last but not least, increased crew safety related to installation, operation, and decommissioning of the floating offshore wind farms.
Honeymooring is a solution for station keeping of floating wind turbines developed by Semar to address these industry needs. Considering the development of the marine operations involved in installing and maintaining large wind farms, it is evident that the processes should be kept as simple as possible.
Honeymooring enables solutions that simplify the procedures, reduce marine operation time and reduce hardware cost while contributing to safer marine operations for the crew.